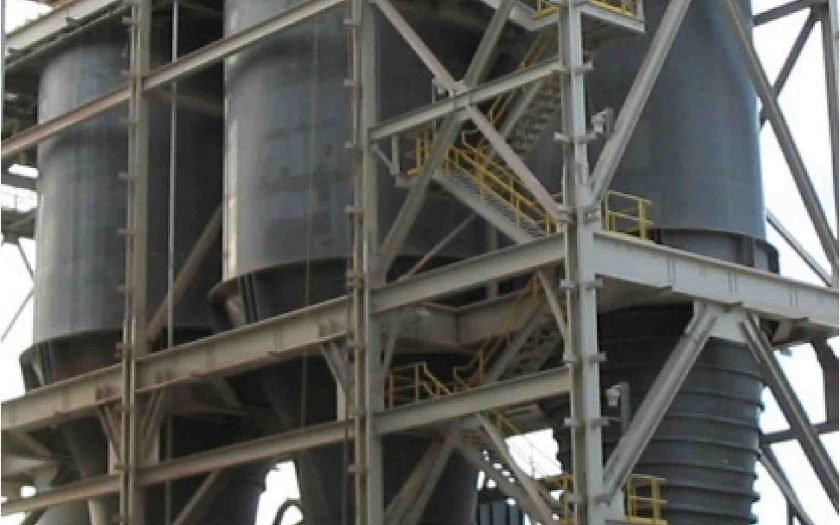
Titan America manufactures Portland cement at their Medley, Florida USA plant, and in June 2004 commissioned a new 5,000 ton per day kiln that greatly increased clinker production capability and efficiency. However, due to poor flowing raw materials handled in the new silos, large variations in raw meal properties resulted, principally from erratic flow of limestone.
Jenike & Johanson engineers visited the new plant to review the solids handling difficulties and to develop a scope of work necessary to alleviate the costly flow problems. The efforts, in part, allowed Titan to eventually exceed design clinker production capacity by 10%.
Jenike & Johanson’s scope of work consisted of:
- an on-site flow assessment (audit);
- material characterization studies and abrasive wear tests with the limestone;
- functional design engineering for retrofitting the existing silo to achieve reliable flow;
- analyses to determine material-induced and external loads on the silo structure; and
- detailed engineering design of the retrofitted silo components.
A discussion of each of these key efforts follows.
Titan requested that engineers from Jenike & Johanson visit the Medley plant as soon as possible to diagnose various solids handling problems occurring during the commissioning of the new line. Engineers observed flow problems, such as arching, ratholing, and segregation occurring with the limestone, as well as other additives like bauxite and mill scale. The flow problems were costly to Titan in several ways: first, the production capability of the new line was less than required; second, there were numerous laborers required to unblock flow obstructions formed in the additive silos; third, the particle size variability of the limestone induced unacceptable chemistry variations (excessive lime saturation factors) in the raw meal; and fourth, valuable resources were redirected to address the ongoing critical problems.
The original blended limestone silo (third silo from the right in photo), has about a 9 m diameter cylinder section followed beneath by a conical hopper then a transition hopper terminating at an apron feeder.
The limestone flow problems rapidly degraded production efficiency, and in some cases, stopped production all together. The bridging problem occurred when an arch-shaped obstruction formed above the outlet of the transition hopper and prevented any further material discharge. Operators were frequently required to use sledgehammers to strike the walls of the hopper to overcome the bridging problem; in many cases, their efforts were not fruitful.
Ratholing in the silo was also resulting, especially when the limestone was fine and wet. With ratholing, flow takes place in a small channel located above the hopper outlet, leaving large zones of stagnant material in the silo. Consequently, even though the silo’s total capacity was 1000 t, its actual “live” capacity was far less; this required operators to vigilantly keep the silo filled so that the raw mix would contain the blended limestone.
Another problem, sifting segregation, was resulting during filling of the silo. This segregation occurs when fine particles concentrate in the center of a silo during filling, while the more coarse particles roll to the pile’s periphery. Since discharge from the segregated pile in the silo occurred from a central core, during initial drawdown, a high concentration of fine particles was reclaimed onto the raw mix conveyor. Unfortunately, with the limestone extracted from the quarry near Titan, as the particle size changed, the chemistry of the material changed; in particular, the silica content varied substantially across the particle size range. As the level in the blended limestone changed, the particle size distribution of the material varied.
The Solution
Material Testing
After the site visit audit, Jenike & Johanson engineers recommended to Titan that flow properties tests be performed on the limestone at moisture contents ranging from 5% to 11%. The flow tests were measured using ASTM protocols. Not surprisingly, the results of the flow tests confirmed the limestone was cohesive (prone to bridge and rathole), frictional (sticks to surfaces), and compressible (having a variable bulk density).
Functional Design Modifications
The flow problems occurring were directly influenced by the type of discharge pattern in the blended limestone silo. Per flow test results and field observations, a funnel flow pattern was resulting, whereby an active flow channel forms above the hopper outlet, with large dead zones of material residing in the silo. As the level of limestone in the silo decreased, the non-flowing material generally did not slide into the flowing channel, which resulted in the formation of a stable rathole.
Jenike & Johanson recommended to Titan that a mass flow pattern be implemented, which allows a first-in, first-out discharge that prevents ratholing, ensures consistent flow, eliminates sifting segregation, and reduces the loads on the apron feeder.
The recommended modifications to the silo involved installing a new, steep conical hopper that extended past the existing cone up into the existing cylinder section. A new transition hopper, pin gate, and mass flow interface was implemented above a new apron feeder. A separate weigh belt feeder was placed below the apron feeder, but oriented to run in the opposite direction so that the feeder allows weighing capability as well as clean-up duty, which eliminated the need for a separate dribble conveyor running
below the apron feeder.
The apron feeder and its interface were properly designed to ensure complete withdrawal of material along the entire length of the hopper outlet, thereby eliminating stagnant material. The increasing capacity along the length is achieved by the increase in height and width of the steel interface above the feeder. Jenike & Johanson engineers worked closely with apron feeder and interface supplier to ensure its structural integrity and functional design specifications were strictly followed. Abrasive wear tests were conducted to assess erosive wear life of various liners for the interior silo walls and the interface.
Analyses were also performed by Jenike & Johanson to determine material-induced and external loads (e.g., wind, seismic, etc.) on the silo and structure. Bulk solids do not behave like liquids since they develop frictional forces against the wall in their static and sliding conditions; this considerably affects the loads on the silo structure. Material-induced loads from initial fill and mass flow discharge scenarios were analyzed.
Detailed engineering
Generally, retrofit projects in silo structures are more complex than new silo construction. In addition to meeting strength requirements, the new components in the silo have to be designed for easy installation and be sized to fit space constraints due to surrounding structures, equipment, etc.
During the structural design phase of the project, it was decided to install the new mass flow cone inside the existing structure without demolition of the existing cone and support system. An arrangement of vertical stringers and rings were designed to facilitate installation of the conical hopper. The conical hopper was designed to be supported at its top edge by welding it to the cylinder. With the location of the new mass flow cone, the load transfer to the supporting structure was modified. The cylindrical portion below the cone top edge was required to carry all the structure and material weight as well as resisting external loading. The transition hopper was designed to be a bolted connection to the adjacent components of the structure, with its pieces to be assembled on-site; this approach simplified installation. The engineering for the arrangement/installation of the steel liner panels as well as their connection details to the new cone and existing cylinder was provided to Titan.
The Result
According to John Anagnostou, production manager at Titan, the modified silo has provided reliable, consistent flow of the blended limestone, even when handling moist and fine material. Since the modifications, mass flow has been achieved which has eliminated the costly bridging, ratholing, and segregation problems. The apron feeder has worked well, and the weigh belt feeder/clean-up conveyor system has allowed fine-tuned control of the raw mix chemistry. Not only were critical details for flow supplied, but also, engineering specifications for demolition, scaffolding, installation, and fabrication were provided to Titan in a complete drawing package.