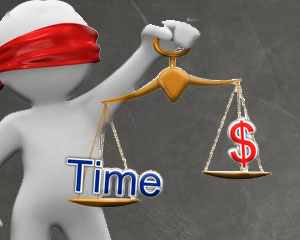
Over the last 3.5 years of working at Jenike & Johanson I have been called to troubleshoot and fix many bulk material handling systems. Most of the time these systems need adjustments because a line designed to handle one material is asked to produce the same material at a higher rate or a completely different material entirely. Usually no new equipment is procured and the only cost to the plant is that due to missed production, or additional operator intervention to get the line to limp along. In these cases we usually can quickly do some analyses and determine whether the line can handle the new rate or material that it is being asked to handle.
In more instances than I would like, however, I am called to troubleshoot greenfield and brownfield projects where a system was procured including new equipment, controls, and in some instances infrastructure. In these cases, the new system was designed using anecdotal experience or by avoiding a particular type of equipment and finding a “better” way of doing it. As you can imagine, these types of situations are usually accompanied by a pretty hefty price tag. When fixing these systems there is an inherent need to “make the equipment work”. And as much as we try to repurpose the equipment we can only do so by compromising performance, reliability, or both. Sometimes repurposing is impossible and new equipment has to be procured in order to achieve the system requirements, increasing the size of the already hefty price tag. In these situations we are usually working under much more pressure and a tighter timeline further increasing cost and in most cases downtime and delaying time-to-market.
So, if you are looking at installing a new system or repurposing an old system, please be sure to keep the following in mind in order to mitigate the pain and suffering I so often witness in our clients:
- Make sure to have a clear understanding of the new (or repurposed) system requirements, including throughput and production rates. Ideally, you would have a complete process flow diagram
- If upgrading an old system, ensure you understand what the “issues” with the old system are; but more importantly ensure that you find an assignable cause for these issues
- Understand the physical and chemical properties of your product(s), especially as they pertain to flow. Bench scale testing of the materials may be enough to provide a clear understanding of flow properties, but in some instances physical modeling is necessary
- Enlist the help of knowledgeable people to determine the most effective way to reach your project goals. Make sure that these advisors help you understand the “why” of their recommendations and that are able to substantiate it
Ensuring proper design of your bulk material handling system components can save you hundreds of thousands of dollars in retrofits, production loss, manual labor, etc. If you have questions regarding how to efficiently design your new system, drop us a line, our engineers are here to help you!