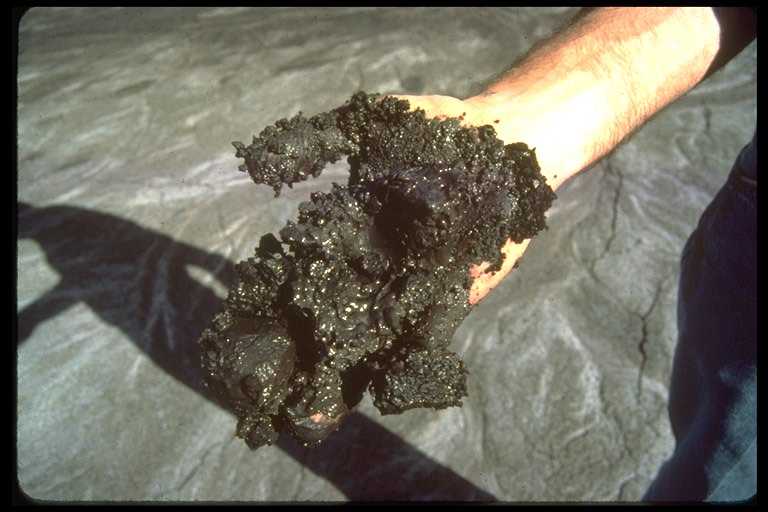
The Need
A major US conglomerate ships petroleum coke throughout the Pacific Rim. Delays in the loading operation created by flow stoppages can disrupt schedules, leading to higher shipping costs.
The facility encountered severe plugging problems with the chutes that feeds into their main storage silos. These stoppages occurred in several chutes at conveyor transfer points. The water used in cleanups ended up in the silos, which increased the moisture content of the stored coke and thus created additional clean-up problems downstream.
A tripper car chute in the ship loading system also experienced similar problems. Blockages at this location, where flow rates at times reach 2,000 tons per hour, sometimes halted ship-loading operations for an entire shift.
The Solution
Flow testing on various samples of petroleum coke allowed J&J engineers to evaluate the cause of chute plugging. A thorough review of the transfer chute system was performed. It was determined that the chute design needed significant modifications to maintain reliable stream flow.
A new chute geometry was developed, including a diverter (flop gate) feature. J&J was also contracted to develop mechanical fabrication drawings and supply of the new chute, which has several key features for maintaining sticky coal flow. Abrasive wear testing was also done by J&J to evaluate chute liner life.
The Result
The petroleum coke handling system has been in operation for over three years with minimal downtime for maintenance.