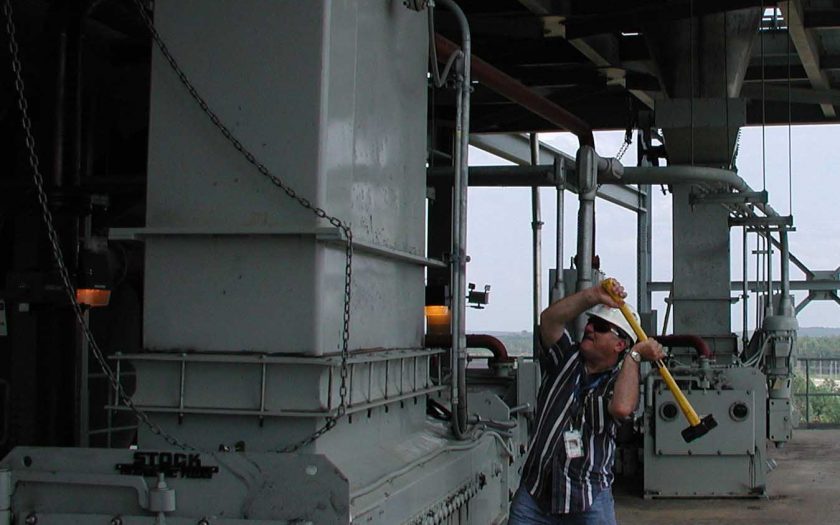
The Need
Northern States Power (NSP) has a 384 megawatt coal-fired power plant in Minneapolis, Minnesota with coal bunkers built more than 30 years ago. Little consideration was given during the design stage to the flow properties of the coal. As a result, flow problems could be expected, even when handling what is considered to be relatively free-flowing bituminous coal.
After switching to a low sulfur sub-bituminous coal, NSP experienced several fires and one explosion in its unit 7 coal bunker. Immediately, a task force known as “Operation Cease Fire” was set up to investigate and eliminate the spontaneous combustion problem in all of NSP’s plants.
The problem was determined to be the funnel flow discharge pattern of sub-bituminous coal through the bunkers. The first-in last-out flow sequence allowed stagnant regions of coal to remain indefinitely. Such stagnant coal is highly susceptible to spontaneous combustion.
The Solution
The solution to a funnel flow problem is to convert the discharge pattern to mass flow. With mass flow, all of the material is in motion which provides a uniform residence time for all of the material.
Samples of the sub-bituminous coal were sent to our lab for flow properties tests, using the widely accepted Jenike Shear Tester. With cohesive strength and wall friction data now available, our engineers were able to recommend hopper modifications that would provide mass flow to the existing bunkers.
Due to economic constraints, NSP decided to modify only one bunker. The modifications first involved replacing the lower portion of a series of pyramidal hoppers with conical hoppers and the valleys in the upper portion of the pyramidal sections were filled in with flat plates in order to provide a steeper slope.
Because headroom was limited, we recommended a BINSERT® system. Properly designed, such a cone-in-cone design enables mass flow to occur with angles that would not normally be steep enough.
For this application, our tests showed that TIVAR® 88 (UHMW polyethylene) was less frictional than either mill finish carbon steel plate or stainless steel sheet with a 2B finish. Therefore, all of the remaining existing hopper sections and modifications were lined with UHMW.
The Result
Northern States Power was able to realize a 64% increase in “live” storage capacity of the coal handled in the modified bunker. The bunkers originally designed to handle bituminous coal are now able to handle more cohesive Powder River Basin coal, and coal fires and dust explosions have been eliminated.