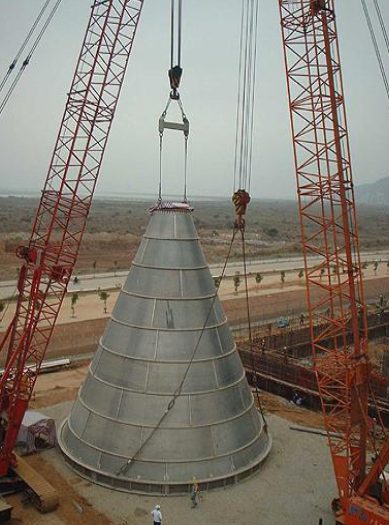
The Need
A client of Jenike & Johanson was expanding storage and handling capabilities for purified terephthalic acid (PTA). As part of the expansion, an existing silo would be retrofitted with a new mass flow transition hopper. The basis for the design of the new hopper was a similar hopper, designed and supplied by us that was handling the same material. This hopper had been performing as intended since it was installed more than 20 years ago.
The design was sent out for bids but since its top diameter was only 10′, the unit could be shop fabricated. Several pieces of existing equipment would have to be temporarily removed so that the new hopper could be installed. The estimated cost for relocating this equipment was significantly more than the cost of the hopper itself.
When evaluating any equipment bid, consider how well each bidder understands the requirements of the job. Not knowing the design intent and requirements for providing reliable material flow typically results in an underbid for the equipment. Sometimes the result is an extremely high bid.
Our client contacted us again for assurance that the equipment would work as intended, so the new hopper would handle the material at a higher discharge rate.
The Solution
After our site visit, we recommended small but critical changes to the previous design to ensure that the higher discharge rate could be achieved. These recommendations were based on recent flow properties tests performed to ensure that the material’s handling characteristics had not significantly changed over the last 20 years since it was first tested.
We then designed the transition hopper in sections that could be bolted together. This allowed installation with minimal equipment relocation costs while still ensuring reliable flow. Although the redesigned hopper was more expensive, the total installed cost was reduced by about 50%, since less equipment had to be temporarily removed for the installation.
Jenike & Johanson was awarded the contract for the structural/detailed design and fabrication/supply of the hopper sections. We delivered the equipment on time by working on the design details and fabrication simultaneously.
The Result
Jenike & Johanson was awarded the contract for the detailed design and fabrication of the hopper sections. We delivered the equipment on time by working on the design details and fabrication simultaneously. The new hopper has been in operation for several years. Our client describes it as one of the most reliable parts of the operation.