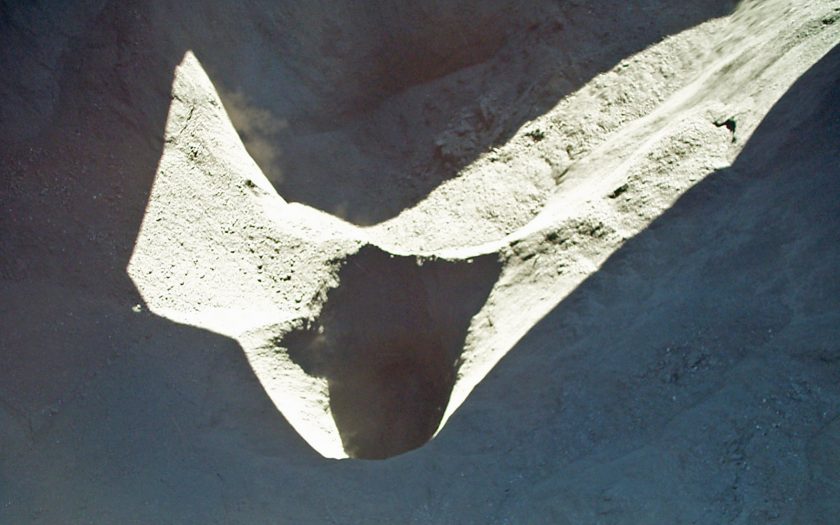
Kaiser Aluminum & Chemical Corp. produces alumina trihydrate which is calcined to make alumina, or it is dried and sold as hydrate. In addition to these two end products, Kaiser wanted to sell its wet alumina trihydrate.
Kaiser needed a new, dedicated handling and storage system. According to Chess Millburn, a project engineer at Kaiser, “The handling characteristics of the wet alumina trihydrate were unknown to us. Just looking at the material, you could tell it was very different than the dry product. There was a general feeling among the plant personnel that we would have major difficulties handling it.”
Alumina trihydrate is used in the manufacture of aluminum chemicals such as aluminum sulfate, aluminum chloride, aluminum fluoride, and sodium aluminate. It is also used as a fire retardant and flame suppressant filler in plastics, a polishing agent, and as a raw material in catalyst and zeolite production.
Kaiser’s engineers determined a silo to be the best means of storage, providing the material could be reliably handled.
The Solution
After Jenike & Johanson’s site visit, it was decided that the next step was to test a sample of the alumina trihydrate in our lab, duplicating the process conditions.
We found that the wet cake was cohesive enough to arch and form stable ratholes in funnel flow silos and that a third flow pattern, expanded flow, would be most suitable. Expanded flow combines mass flow and funnel flow and consists of a mass flow section at the bottom of the silo, extending up to a large enough diameter to prevent the formation of a rathole. Above this mass flow section, the silo is designed for a funnel flow pattern.
Jenike & Johanson’s recommendation for the expanded flow silo is shown in the figures. A mass flow screw feeder was recommended for discharging material from the silo. To achieve mass flow in the transition hopper, the feeder was designed to withdraw material uniformly from the entire outlet of the hopper. This was achieved by ensuring that the capacity of the feeder was increased in the direction of flow.
With mass flow occurring in the lower section of the silo, alumina trihydrate would flow along the hopper walls. Wear was a concern, as alumina trihydrate is an abrasive material. We conducted tests to measure abrasive wear on the selected hopper wall surface, and we calculated the wear life of the hopper walls at the critical areas where high loads and/or high flow rates occur. It was determined that the alumina trihydrate was not very abrasive on the recommended wall material, so the selected wall surface would last for many years.
Our engineers calculated pressures exerted on the silo walls by the stored bulk solid. We analyzed two different conditions: loads applied after the initial filling of the silo, prior to any material discharge, and loads after material had started to discharge (flow loads).
The Result
Kaiser installed the recommended silo and load out bin and they have been reliably handling the wet alumina trihydrate since startup.