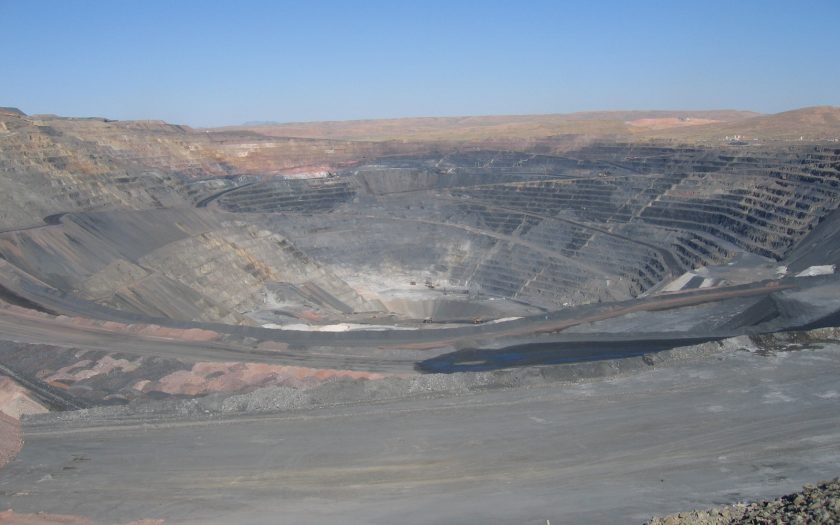
The Need
Part of a modernization project for Chino Mines Company involved new bins for copper concentrate, flux, and slag. Stearns Catalytic Corp., the engineering/construction contractor for the project, asked Jenike & Johanson to evaluate the design of the bins and feeding arrangement.
The design called for four 12′ diameter copper concentrate bins, two 12′ diameter slag bins, and four 7′ 9″ diameter flux bins, all with 35° (from vertical) conical hoppers. An air injection system and a pinch valve in the bottom of each bin were intended to control flow onto an impact flow meter. The material would then be transferred by screw conveyor to the process.
Jenike & Johanson determined the flow properties of the concentrate, flux and slag, each at two moisture contents. Our tests showed that much steeper hoppers (13° from the vertical) would be required to ensure mass flow. Without mass flow, semi-stable ratholes could form even when the moisture contents were low, causing erratic flow. If the moisture content increased above the specified value due to a disturbance in the dryer, arches and ratholing could be expected.
The Solution
A straight mass flow cone inclined at 13° from vertical would have required a substantial increase in headroom. The solution we proposed was to modify the bins with a triple cone BINSERT® system as shown in the sketch. This converted the bins to mass flow, with no increase in headroom. Discharge is controlled by a mass flow screw feeder whose speed is varied by a signal from the impact flow meter.
Although some of the materials are abrasive, screw feeders are viable for this situation because of the low flow rates required and because of the enclosed design of the feeders. Our wear evaluation showed that a reasonable wear life could be expected.
The Result
Jenike & Johanson engineers performed the structural design calculations and prepared engineering drawings for the modification, including the mass flow screw feeders. We reviewed the bin and feeder construction in the fabrication shop and again on-site after installation to ensure that the design was properly executed. We also designed and supplied special shutoff slide gates to be used when performing maintenance on the bins.
The bins have been used for several years and have operated extremely well.