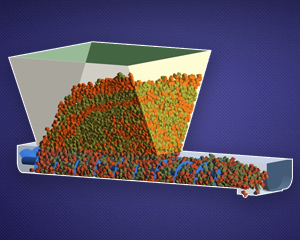
Many of you may recall hearing Al Pacino’s Michael Corleone of the legendary Godfather series say, “Just when I thought I was out, they pull me back in…”
We engineers at J&J can almost hear some of the problematic bulk solids feeders we’ve come across whispering to us, saying, “Just when I thought I could pull the material out, it arches, I interrupt the flow pattern in the vessel and prevent reliable discharge, the material segregates, I cannot meet discharge rate requirements, the material floods uncontrollably out of the hopper outlet, or I have excessive torque and power requirements…”
OK, so maybe there isn’t much of a relationship between Michael Corleone and a bulk solids feeder, maybe I’m terrible at making jokes, and maybe both are true. However, bulk solids feeders – such as screw feeders, belt feeders, rotary valves, vibrating pan feeders, etc. – are just as important to your bulk solids handling operation as Michael Corleone was to the Corleone family. We generally find that storing materials is not the problem – for the vast majority of our clients, the really hard part is getting the material out of the vessel reliably without causing additional solids handling problems.
The feeder is a critical element in any bulk solids handling vessel, since not only does the feeder control how quickly a solid is discharged, but a poorly-designed feeder can also wreak all sorts of havoc in the vessel above, even if the vessel itself is properly designed. Storage vessel design and feeder design are really two halves of the same coin; one cannot function properly without the other!

When a feeder is incorrectly designed or not properly interfaced with its vessel, it can turn mass flow into funnel flow and allow stagnant regions to form, induce arching or ratholing, cause or increase segregation effects, allow uncontrolled flooding of aeratable fine powders, and potentially result in a myriad of other problems that can impact product quality and bottleneck production. A poorly-designed feeder may even cause premature structural failure of the vessel due to formation of a preferential flow channel, as shown in the accompanying pictures; if the vessel was not designed to handle eccentric flow loads, structural failure may occur.
Therefore, if you or someone you know has a bulk material handling problem in a storage vessel, it may not be a problem with the storage vessel itself – the feeder may be to blame! We at J&J have the experience and knowledge to assist you by considering your plant and
operational constraints and the material flow properties to provide you with functional design recommendations for a proper design for your storage vessel and feeder. To learn more about our services and how we can help add value to your plant, contact us.
In later blogs, we’ll discuss many of the specific problems that we often see with belt feeders, screw feeders, and rotary valves.
If you have an immediate need make sure to contact us and we can begin to help!