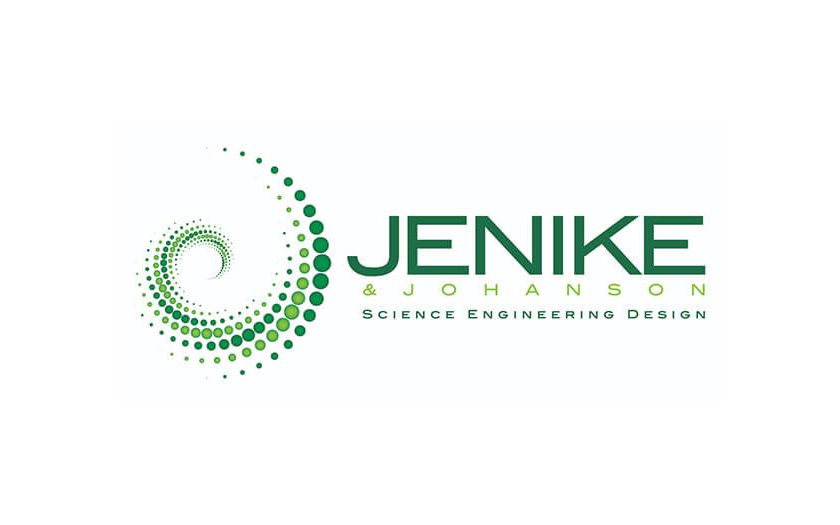
Gathering physical properties of liquids or gases is usually straightforward. For example, if I needed a fluid’s viscosity and specific gravity to design a system for handling a liquid or gas, I need only to perform a Google search or open up a handy handbook. The viscosity of glycerin will be the same whether it came from New Jersey or New Guinea. Bulk solids are another matter. For example, a simple property like bulk density is highly dependent on the powder’s particle size distribution, not to mention that bulk solids are generally compressible.
To design solids handling equipment such as hoppers, silos, bins, chutes, and feeders, I need to measure the cohesive strength, wall friction, compressibility, and permeability of the actual material that is to be handled. I can’t get data from a book or the web. I need to get my hands on the actual material.
Most of the time, my client will provide me a sample of material that I can test in our lab. Because I need data that are representative of the actual process conditions, I sometimes must conduct tests at temperatures and relative humidity that are not ambient. Moisture content often affects flowability, and in some cases, I will test the materials over a range of moisture levels.
Sometimes my client is unable to ship me material because it is hazardous. Other materials may have a short shelf life and must therefore be tested immediately after it is removed from a process. In this case, I need to measure the fundamental flow properties of the bulk solid at the client’s site.
I vividly recall one occasion where I performed shear cell tests at a plant where explosives were manufactured! Needless so say, I was very cautious. During each test, I would place a small sample of explosive powder inside a cell, consolidate it, and then shear it until it failed. This shear cell test allowed me to measure the material’s cohesive strength over a range of pressures. Other tests allowed me to measure wall friction, which is important for applications where mass flow is important and sifting segregation needs to be mitigated.
I managed to complete the tests without incident. Unfortunately, when I was packing the equipment for its return to my lab, I had left a sheet of bubble-wrap on the floor and stepped on it. The sound of fireworks is not what you like to hear when you are at a site that makes explosives.
Not surprisingly, when I arrived at the airport during my trip home, I tested positive for explosives. I explained to the TSA agents that I was an engineer who specialized in bulk solids handling, and that I had spent the day at an ammunitions plant. After the agent interviewed me further, inspected my luggage, and all but gave me a physical, he allowed me to board the plane. A flight attendant asked me if I’d like to sit in Business Class. I like to think that it was the airline’s way of apologizing for my inconvenience, but in reality, I am glad that it was a short flight. I’m sure that if I had gotten up to use the rest room, I would have met the air marshal.
Getting representative data was a little more challenging than I had anticipated, but it was worth the effort. I was able to provide a design that ensured reliable flow and minimized segregation of propellants.