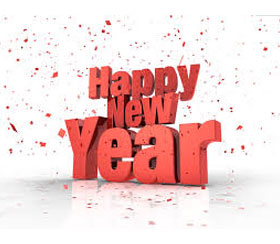
It’s that time again – a new year is upon us providing a fresh start. Our bellies are full of treats and our minds have had time to rest. We reflect on all that was accomplished in 2016 and plan for what is to come in 2017.
As part of reflection, it’s important to evaluate what the missed opportunities in 2016 were – particularly related to downtime caused by solids handling problems. That includes calculating the cost of those nasty unplanned downtime hours. Tracking the cause of those downtime hours is the first step.
The next step is to identify what process improvements can be made to reduce those downtime hours. Improving operational efficiency can help you meet your yearly goals and achieve the next level of processing success.
For example, if you have a chute that plugs enough times that you have to continually staff an operator to monitor and unplug the chute, it might be time to fix the chute. Or what if your chute is wearing out in between shutdowns such that an intermediary shutdown is required just to change out the chute? It may be time to investigate ways to design the chute to reduce wear to extend the life of the chute. Maybe your hopper has been so deformed from being banged on by a sledgehammer that it is time to find a permanent solution.
But what is the best approach for making those changes? There are three main approaches: trial and error, copy and paste, or a scientific approach.
Trial and error – if your flow problem is a minor nuisance, time is not an issue, and it is fairly easy to make a change without costing the company downtime, then maybe a trial and error approach is appropriate. The trial and error approach may take a significant amount of time and money depending on the success of each trial.
Copy and paste – if you have a sister plant successfully handling the same exact material at the same exact moisture content, particle size distribution and temperature with identical processing steps, then investigating what works at the sister plant may be beneficial. But if the material or process is different, there is a risk that the change may not be as effective. As such, a full analysis should be performed to ensure that the change would work. All too often, copy and paste strategies end in having larger problems than the problems intended to be eliminated and it becomes a costly first step of a trial and error approach.
Scientific approach – if your problem is costing significant money due to downtime, safety hazards, and/or rejected product, then you likely want to solve the problem correctly the first time. If that is the case, then a scientific approach based on the flow characteristics of your material is required.
First it is critical to understand the underlying cause of the problem. For any problem, some simple questions can help pinpoint the underlying cause or change that occurred to create the problem. Questions such as:
- When did the problem begin? Or has it always been around but is getting worse due to higher throughput or maybe material value has increased bringing attention to the problem?
- What changed with the material?
- For example, a new supplier or same supplier with a new process, change in chemical composition, particle size shift, increased stickiness, more fines, different blend, particle shape change, etc.
- What has changed in the upstream process?
- For example, fines created by attrition in the upstream process (surface mining vs. blast mining), added preprocessing step that is causing attrition (more screening or crushing steps, more transfers or handling steps). Is material sitting in the surge bin for longer periods of time? Has the processing temperature changed? Has the efficiency of upstream equipment declined such as a dryer resulting in increase moisture content of the downstream material or the dryer being run at higher temperatures?
Once the underlying cause of the problem has been identified, a path forward can be determined. All areas of the processing unit should be considered as changing one part of the process could result in a negative change downstream.
With our 50+ years of experience, we at J&J can help you answer those tough questions and establish a path forward. Material flowability testing will provide the design basis needed to develop the most viable option(s) to resolve the problem(s). The decision of what to change can be made with confidence based on scientific data rather than trying something and hoping that it will work.