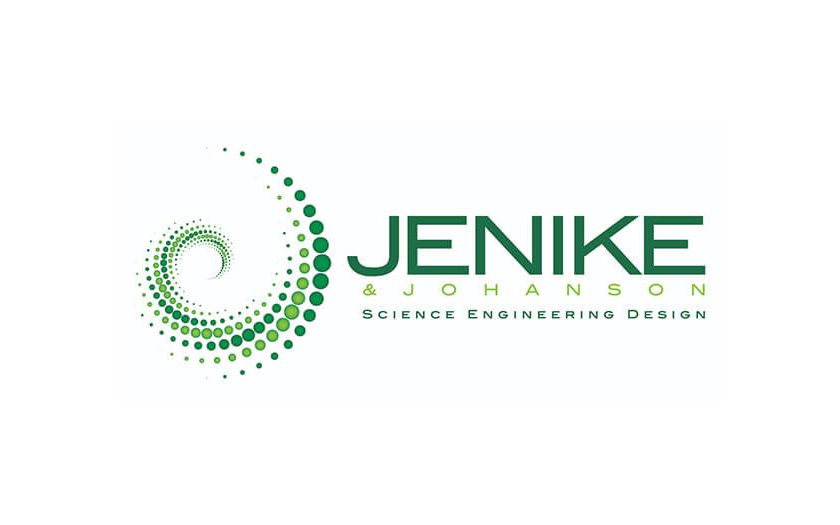
So, now that I have your attention, I’ll admit that I have geeky affinity for modeling solids handling processes.
The challenge of developing a model for part of a process to validate predictions or to develop a design always interests me. Even though I’ve been doing this for over 30 years, each new problem is unique and interesting. Bulk solids are complex materials that can behave like rigid elastic solids, plastically deforming materials and fluids – sometimes all in the same system. Combine this with gas and/or liquid in a system, and complexity increases significantly. The methods we use to characterize and analyze bulk solids can tell us a lot about how bulk solids behave, and in many applications we can use this information to provide a complete design solution or identify the cause of a problem. But some questions can’t be answered adequately through bench scale testing and analysis alone. This is where modeling can provide the necessary information. At J&J we’ve modeled systems from full scale to fractional scale to investigate behavior and develop design criteria for a wide range of applications. We’ve modeled hundreds of systems over the years; a few examples of projects are described below.
During the oil shale development years of the early 80’s we modeled systems for recirculating heat transfer media, up-flow reactors for petroleum extraction, plows for contouring the top surface of a pile in a reactor, seal legs for pressure let down and inclined sealing screws. All of these modeling systems required careful consideration of the key parameters being studied and attention to the model parameters to make sure that the reduced size of the model didn’t bias the results. These models were run at a significantly reduced scale to allow investigation of many variables in systems that would be scaled to hundreds or thousands of tons/hour throughput.
At the other end of the scale are pharmaceutical and food applications. We have modeled systems at full scale to evaluate and design systems for feeding micro-doses of pharmaceuticals into drug-delivery systems, delivering seasonings for food products and filling single-serving packages.
We’ve modeled systems involving gas-solids flow, liquid-solids flow and three-phase liquid-solid-gas systems. Some of these have been continuous recirculating models while others have been batch systems. Often the questions our clients have require modeling part of a process that involves a reaction or process chemistry in addition to the physical interaction of the bulk solids with other media. We have run models up to about 1,100°F and others cooled with liquid nitrogen; some have included purging with hydrogen, CO2, and nitrogen; and we’ve run solid-liquid models with paraffin based liquids, sugar solutions, hydrocarbon solvents and water. Pressurized models have been built for pressures from a few hundred psi, up to 1,000 psi, as well as for vacuum of a few millimeters of mercury.
When I started at J&J we had a single story building and occasionally had to use the roof to get enough height to set up a tall model. Shortly after I joined J&J we opened our California office, which was specifically built with a world class modeling facility including a 4,000 square foot, two-story lab, an overhead crane and a pit that allows plenty of room for most models.
Recent development of usable, practical [modal destination=”http://www.youtube.com/watch?v=RR1ItrumiHA” link_text=”Discrete Element Modeling” caption=”Jenike & Johanson DEM analysis of transfer chute design with a rock box” media=”video”] software has reduced the need for some kinds of physical models, but bulk solids are some of the most complex materials we encounter, and it will be a long time before DEM can adequately model the complex interactions of real materials and eliminate the need for physical modeling.