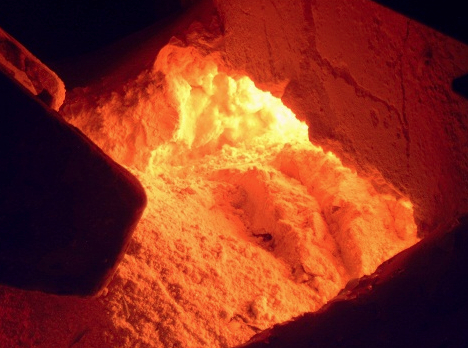
The Need
Libbey Glass is the leading producer of high quality, machine made glass tableware in North America.
The soda-lime glass used for beverage glasses is primarily composed of silica, limestone, soda, and cullet (crushed, recycled glass). This mixture is referred to as “glass batch.” The glass batch ingredients are weighed and blended before they are fed into a storage bin and then melted in a furnace. Molten glass is drawn from the furnace and delivered to molding and forming equipment, where the glass is progressively formed into finished tableware, heat treated, and cooled.
A major furnace rebuild included a new batch charging system and replacement of the glass batch storage bin. The quality problems began after completion of this rebuild. Following the furnace startup, the plant experienced several occurrences of glass quality deterioration that were traced back to relatively minor batch plant downtime events. The glass quality issues of cord (variations in glass composition that result in a visual blemish or residual stresses), seeds and blisters (gas bubbles), and composition shifts appeared to be classic examples of batch segregation. On several occasions, the magnitude of the upsets were great enough to cause total production loss. Libbey’s investigation of the batch weighing, mixing, and transfer systems did not turn up any significant problems. The mixed batch storage bin, however, showed dramatic signs of segregation, which increased in magnitude when the batching process was suspended for a period of time.
The Solution
After Jenike & Johanson’s site visit, a sample of Libbey’s glass batch was sent to our testing lab so that the flow properties of the glass batch could be measured. These measurements and a review of the existing equipment drawings, confirmed that the geometry of the batch bin was contributing to the quality problems experienced in Libbey’s finished products. The measurements also provided the information needed as a design basis for recommending a solution.
Segregation of the components of a blend by the sifting mechanism is likely if the following conditions are present:
- The material is free flowing.
- A sufficient range of particle sizes is present in the blend.
- The material is sufficiently coarse.
- There is inter-particle motion.
When loading material into the batch bin, all of these conditions were met, and sifting segregation occurred. This resulted in a concentration of fine material under the fill point (in this case, the center of the bin), as the fines sifted through a matrix of coarse particles.
Two flow patterns can exist in a bin during discharge. “Funnel flow” is the term used to describe the condition where flowing and stagnant regions of material exist concurrently within a bin. “Mass flow” is achieved when all of the material in the bin is in motion during discharge.
One of the advantages of mass flow is if a blended material has segregated in a horizontal manner as it is loaded into the bin, it will be recombined at the outlet, since material is withdrawn from along the wall as well as from the center of the bin. When a funnel flow bin with a center fill and center withdrawal is used, and this type of segregation is present, significant variations in the composition of the discharge can be expected as the level in the bin changes.
In order to achieve mass flow, the outlet must be large enough to prevent the formation of an arch, and the hopper walls must be steep and smooth enough to allow the material to flow along them. The hopper wall angle required varies dramatically from bulk solid to bulk solid, and is highly dependent on the wall material and surface finish and, potentially, on such things as moisture content, particle size, and chemical composition. Measuring the actual flow properties of Libbey’s glass batch eliminated guesswork and provided a sound design basis for recommending a solution to the segregation problem. Our tests confirmed that the existing bin was operating with a funnel flow discharge pattern, and, more importantly, provided the information necessary for recommending a solution.
A BINSERT® hopper retrofit was recommended to convert the existing batch bin to mass flow and to control segregation. We developed the BINSERT® system to control and expand flow patterns in bins by using a mass flow hopper-within-a-hopper. The inner hopper is designed to provide mass flow through the central channel and also through the annular space between it and the outer hopper.
We also provided the equipment necessary for the retrofit. This consisted of a replacement lower hopper with an inner cone, support beams, and a liner for the portion of the upper hopper that was to remain. The retrofit was designed specifically for Libbey’s installation and for the material being handled. We then provided assistance to the installation contractor to ensure that the job was completed correctly.
The Result
As a result of the changes made to the batch storage and delivery systems, the quality problems that had been plaguing the plant since the last rebuild have been eliminated.
Another benefit realized after the retrofit was an increased live storage capacity.