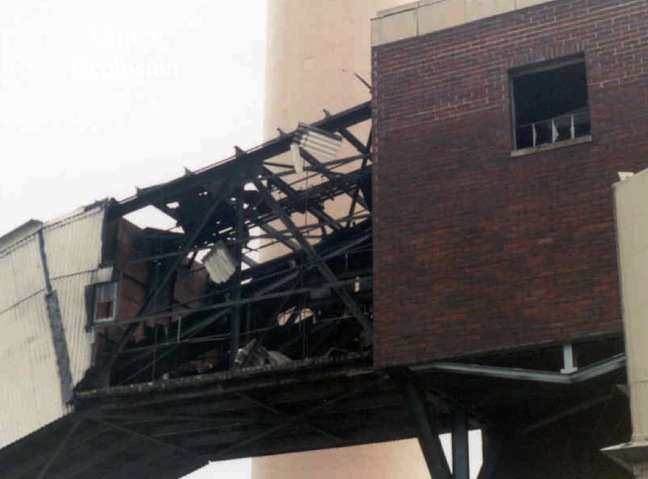
The Need
Wisconsin Public Service’s Pulliam Station has six active units totaling 375 MW capacity. The original plant was built in 1926. Back then, as a result of wide availability of coarse, low moisture, bituminous coal, limited consideration was given to coal flow. Design factors centered around corrosion and abrasion resistance. This often resulted in funnel flow design of silos and bunkers, as was the case at Pulliam Station. In 1991, Pulliam Station changed fuel, and switched to PRB coal. Shortly after, the Station experienced a tripper floor explosion that was triggered by a bunker fire in a coal mine. PRB coal had ignited spontaneously and led to an explosion. After this explosion, the Station personnel were faced with a challenging question: how to eliminate stagnant coal in the bunkers.
The Solution
Jenike & Johanson (J&J) was hired to evaluate coal handling system in Units 5 and 8. J&J performed a coal flow study; analysis of the flow properties test results indicated that both Unit 5 and Unit 8 coal bunkers were funnel flow, and resulted in formation of stagnant coal regions within the bunkers. J&J recommended converting the existing funnel flow bunkers to Mass flow, which would eliminate stagnant coal and decrease the potential for bunker fires. Converting the Unit 5 bunkers involved removing the entire conical hopper section and installing a new symmetric 2-stage conical hopper. Converting the Unit 8 bunkers involved replacing Gunite coating with TIVAR®, and improving the valley angles in pyramidal hopper sections by using valley plates.
The Result
By modifying the Unit 5 bunkers, the coal flow pattern changed from funnel flow to mass flow. Coal flow has been reliable and the fuel switch to PRB coal has been successfully implemented. In the Unit 8 bunker also, the flow pattern was changed to mass flow.