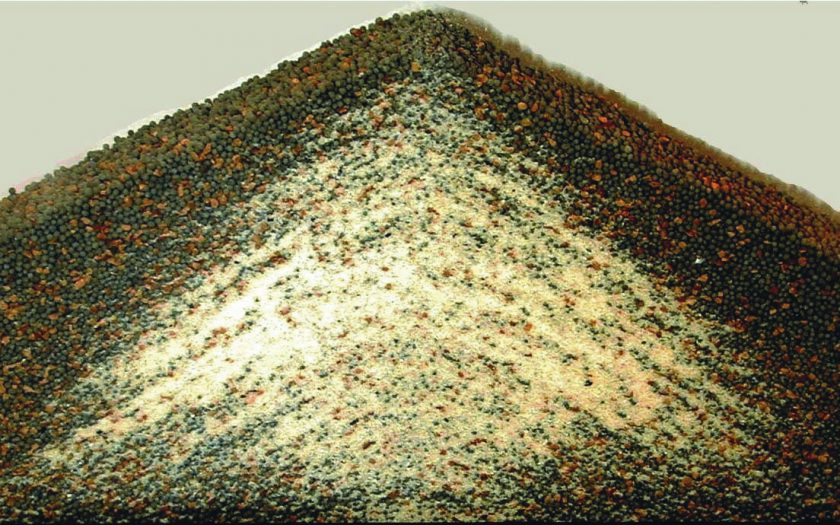
Material segregation is a multifaceted headache. It disrupts bulk material handling with all manner of adverse effects. Loss of process efficiency is one of the most common issues you’ll face due to material segregation. But even this issue is many-sided. It may be that material segregation causes blockages or uneven flow rates. The resulting wear-and-tear could lead to avoidable downtime for repairs—impinging on your ability to conduct predictive maintenance.
Fortunately, a large part of combating material segregation is understanding the various mechanisms causing bulk materials to separate.
What is Material Segregation?
Material segregation refers to the separation of particles within a bulk material. This is based on the differences in their physical properties, such as size, shape, density, or resiliency. Material segregation occurs in various stages of material handling, including storage, conveying, and packaging. It appears due to numerous factors, including particle size differences, handling techniques, and the properties of the materials themselves. The effects of material segregation are often detrimental, leading to inconsistencies in product quality, difficulties in processing, and increased waste.
Common Segregation Mechanisms
Several mechanisms contribute to particle segregation. Understanding these common segregation mechanisms is key to addressing the challenges they present:
- Sifting Segregation: One of the most prevalent forms, sifting segregation occurs when particles of varying sizes separate due to gravitational forces. When bulk material is discharged to form a pile, larger particles, known as coarse particles, roll down to the periphery, while smaller particles, including fine particles, tend to remain in the center. This type of segregation is particularly common in processes that involve piling materials or filling bins.
- Fluidization Segregation: Fluidization segregation occurs when fine particles become airborne because of air entrainment and separate from larger particles. This phenomenon is often seen in processes that involve high air velocities. These include pneumatic conveying or when materials are poured from a significant height. As the fine particles are lifted by the airflow, they settle in different locations from the bulk material, leading to segregation.
- Dusting Segregation: This is a type of fluidization where the smallest particles become suspended in the air during handling. These fine particles then settle separately from the bulk material, often leading to contamination and product loss. Dusting segregation is particularly problematic in industries that handle fine powders. It can be mitigated through proper dust management systems.
- Trajectory Segregation: Trajectory segregation occurs when particles of different sizes and densities are projected from a conveyor belt. Due to differences in their trajectories, larger and heavier particles tend to travel further. However smaller particles drop off sooner. This can lead to a gradation of particle sizes along the length of a pile, further exacerbating segregation.
Factors Contributing to Material Segregation
Several factors influence the degree to which segregation occurs in bulk materials:
- Particle Size: The most significant factor is the difference of particle size in the bulk material. With a wide range of particle sizes, smaller particles tend to migrate differently than larger particles, leading to segregation. Fine particles, due to their small size, may become airborne or settle differently than coarse particles, exacerbating segregation effects.
- Shape and Density: Variations in particle shape and density can also contribute to segregation. Particles with irregular shapes or different densities may move differently within a pile or bin. This causes them to separate from other particles.
- Angle of Repose: The angle of repose, or the steepness of a pile, can affect how particles segregate. Materials with a low angle of repose are more likely to experience sifting segregation as coarse particles roll down the slope more easily than smaller particles.
- Material Handling Equipment: The design and operation of material handling equipment, such as conveyors, chutes, and bins, play a crucial role in how segregation occurs. Equipment that does not control the flow of material effectively can exacerbate segregation issues. For instance, bins that promote funnel flow are more likely to cause segregation than those designed for mass flow.
Mitigating the Effects of Material Segregation
To address and mitigate the effects of material segregation, it is essential to understand the specific type of segregation occurring and the conditions that promote it. Here are some strategies that can help reduce segregation:
- Optimize Particle Size Distribution: Ensuring a controlled and narrow range of particle sizes can help minimize segregation. By reducing the difference between the largest and smallest particles, the likelihood of segregation is decreased.
- Control Flow Patterns: Designing material handling systems that promote mass flow rather than funnel flow can significantly reduce segregation. Mass flow bins, for example, make sure that material moves uniformly, which helps recombine segregated particles.
- Reduce Air Entrainment: In processes prone to fluidization segregation, controlling air flow and minimizing the height from which materials are dropped can help reduce the separation of fine particles from the bulk material.
- Regular Testing and Analysis: Conducting regular segregation tests and analyzing material flow properties are critical steps in developing effective solutions. By comprehending how a material behaves under different conditions, it’s possible to design equipment and processes that minimize material segregation.
Prevent Material Segregation From Causing Issues With Bulk Materials
Understanding the types of material segregation and their underlying causes is crucial for anyone involved in bulk material handling. By recognizing how material segregation occurs and implementing strategies to mitigate it, companies can improve product quality, reduce waste, and enhance overall process efficiency. Whether through optimizing particle size distribution, controlling flow patterns, or using advanced material handling equipment, addressing material segregation effects can lead to significant improvements in industrial operations.
Discover how to tackle material segregation issues by exploring our detailed solutions and case studies listed on our website.