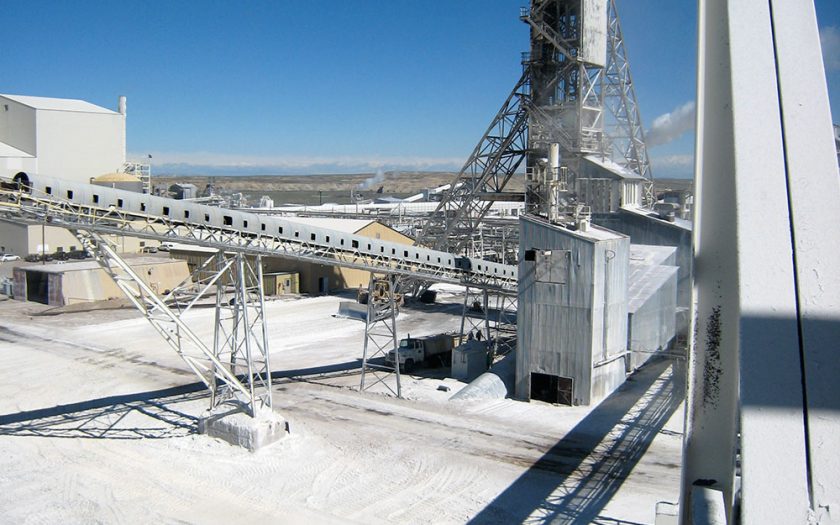
The Need
Engineers at Martin Marietta Magnesia Specialties, Inc. were in the process of designing two steel silos to handle dolomite lime, at the Manistee, Michigan plant. Each silo was to be 21 ft. in diameter by approximately 56 ft. tall with a 30° from vertical cone converging to a 2 ft. diameter outlet. Below the outlet, a round-to-square transition with a slide gate opened onto a vibratory pan feeder/conveyor.
We were asked to evaluate the proposed design to determine whether [popover image=”/your-need/poor-flow/hopper-flow-pattern-mass-flow/” link_text=”mass flow” title=” ” content=”Discharge pattern occurring in silo, bin, bunker, or hopper” direction=”right”] would be achieved, which was required in order to minimize segregation and ensure reliable flow. We received representative samples of dolomite lime from Martin Marietta, and performed flow property tests. The test results showed that this dolomite lime was easy flowing, and thus able to flow through small outlets without forming a cohesive [popover image=”/your-need/poor-flow/hopper-flow-obstruction-arching-bridging/” link_text=”arch.” title=” ” content=”A costly no-flow problem” direction=”right”]
. However, it was also very frictional, requiring wall angles much steeper than 30° (from vertical) for flow to occur along steel walls. We concluded that the proposed design would not provide mass flow when handling this material.
The Solution
The solution we recommended incorporated a unique BINSERT® design. We took the normal cone-in-cone concept one step further with the addition of an internal third cone. In doing so, we were able to utilize the original silo envelope with a 30° cone, thus maintaining the required silo capacity within the same height.
The BINSERT® system is unique in that it allows less steep wall angles to be used, but still achieves mass flow. It works by altering the pressures that are exerted on the walls of a conventional single cone hopper to force the material to slide along the walls, thus creating mass flow.
With a BINSERT® system, segregation can be controlled better than with a mass flow silo with a single cone. The BINSERT® system reduces solids velocity differences, thereby virtually eliminating segregation regardless of the material level in the cylinder.
In order to prevent interlocking of large 2 in. particles of dolomite lime, the minimum outlet diameter of the innermost cone had to be 1ft. Therefore, we had to terminate the outer cone at about a 3 ft. diameter. This change in outlet diameter required a new transition piece to mate with the feeder.
This design eliminated the vibrating pan feeder, and utilized a belt feeder with an interface designed to withdraw material uniformly from the entire area of the outlet.
The overall design was accepted by Martin Marietta, and the two silos were fabricated.
The Result
The overall design was accepted by Martin Marietta, and the two silos were fabricated.