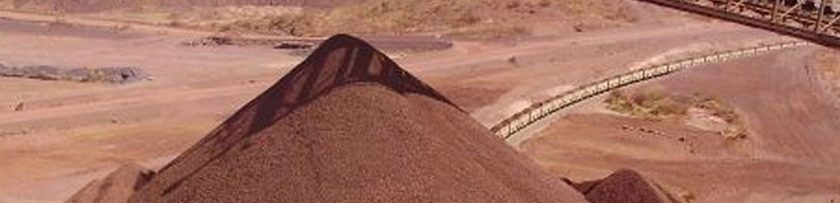
When developing the functional design for a bin, silo or stockpile, the required live (i.e., useable) storage capacity is essential. We often find that the design criteria define the capacity without clarifying if it indicates total capacity or live capacity. In some applications, for instance in a stockpile, the difference between live and total capacity can be huge. Besides the task of figuring out the storage vessel or stockpile dimensions that will ensure the required capacity, the designer must also consider the flow properties of the material to be stored. The design must avoid typical bulk material flow problems , such as arching and ratholing.
Sometimes, defining the live capacity required in a new bin or silo is relatively simple. Consider, as an example, the simplified case of a continuous process that must be fed at 4 tph, 24 h/day from a silo that can only be charged (at 4 tph) during an 8-hour shift. In this case it is easy to show that if one assumes no time is required for maintenance, the minimum live capacity required is 64 t. This value allows the amount of material contained in the silo to vary as shown in Figure 1.
Most cases in reality are not so simple. Normally in a large plant, significant downtime must be considered for maintenance, both programmed and due to unplanned equipment failures. To accurately estimate the required crushed ore stockpile live capacity for large mining projects, we have developed a specialized dynamic simulation program, with a probabilistic approach, that is based on the process flow sheet of the operation, and takes into consideration key parameters such as:
- Flow rates according to design criteria
- Equipment nominal and maximum instantaneous capacity
- Mine schedule (including truck haul time)
- Storm statistics, including frequency and effects on operations
- Maintenance program, time between failures, and statistics about time to repair for each type of equipment (crushers, feeders, conveyors, etc.)
- Holidays in which work is stopped (if any)
To determine the optimum location for concentrate stockpiles in a plant or at a port, we have had to include other parameters such as:
- Railway characteristics, e.g., railcar capacity, number of cars per convoy, travel time, time to unload
- Statistics about ships, e.g., deviations of estimated time of arrival, time for maneuvers, charging time, time to stow
- Statistics about port closures because of storms or rough seas
Developing the program and obtaining the relevant data to run it can be a time-consuming task. However, for large projects, with hundreds of thousands of tons to be shipped annually, avoiding the risk of having to stop production because stockpiles are full, or of having ships waiting to be loaded because there is not enough material in the port to fill them, often justifies the effort.