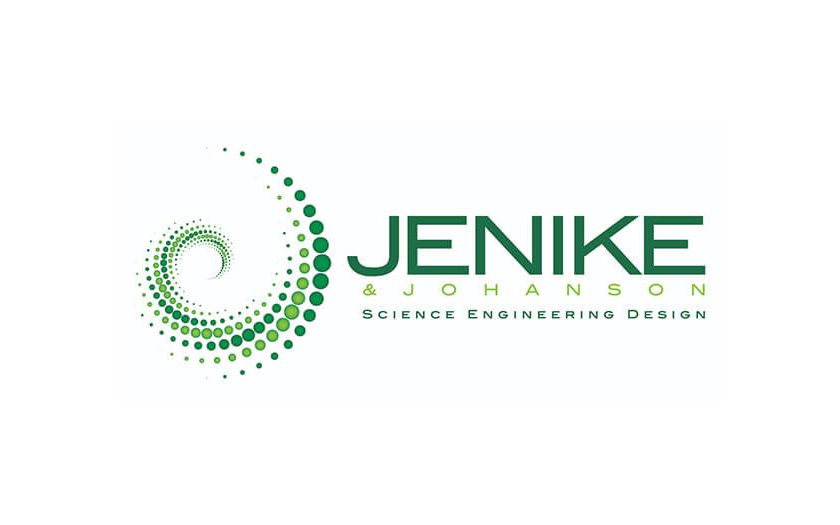
Although continuous manufacturing has been used in other industries for centuries to produce products ranging from glass bottles to breakfast cereals, it is still in its infancy in the pharmaceutical industry. This situation has often prompted the question among pharmaceutical companies, vendors and regulatory agencies: “If continuous manufacturing is routine for other consumer products, why can’t we do it too?” Potential obstacles such as transforming traditional batch processes to continuous processes, maintaining process control and potential regulatory challenges all seemed daunting.
However, judging from the recent presentations at the 2015 IFPAC annual meeting and the AAPS Arden Conference, major advances have been made to implement continuous manufacturing in the pharmaceutical industry for both prescription and over-the-counter products. This achievement is largely due to a collaborative effort by pharmaceutical companies, equipment vendors and regulatory agencies to facilitate developments that seemed impossible as little as a decade ago. The evolution of process analytical technology (PAT), advanced process control (APC), process modeling methods and continuous manufacturing equipment have aligned in highly synergistic ways.
Many of the presenters at the 2015 IFPAC annual meeting and the AAPS Arden Conference stressed the importance of measuring material properties and using them as inputs in process models as a cornerstone to an approach for robust continuous manufacturing. This message certainly resonates with us at Jenike & Johanson, since our very inception as a company was based on the fundamental questions of: What material properties define how a powder “flows” and how can these properties be used in predictive models?
The possibilities of continuous manufacturing in the pharmaceutical industry are exciting, but many common powder handling challenges persist, including:
- How can I ensure my cohesive, milled API flows reliably?
- Will I be able to feed my blend components to my blender/granulator at a stable target feed rate?
- Can my product be reliably pneumatically conveyed between process steps?
- Are there segregation risks downstream of the final blending process that can affect content uniformity?
- Can I meet my target compression rates?
Jenike & Johanson is ready to assist you as your company embarks on transforming your traditional batch processes to continuous manufacturing, so please [modal_contact link_text=”contact us”] if you would like to discuss your goals and challenges further … or just drop by our booth at Interphex 2015 (#3913) and we’d be happy to speak with you.