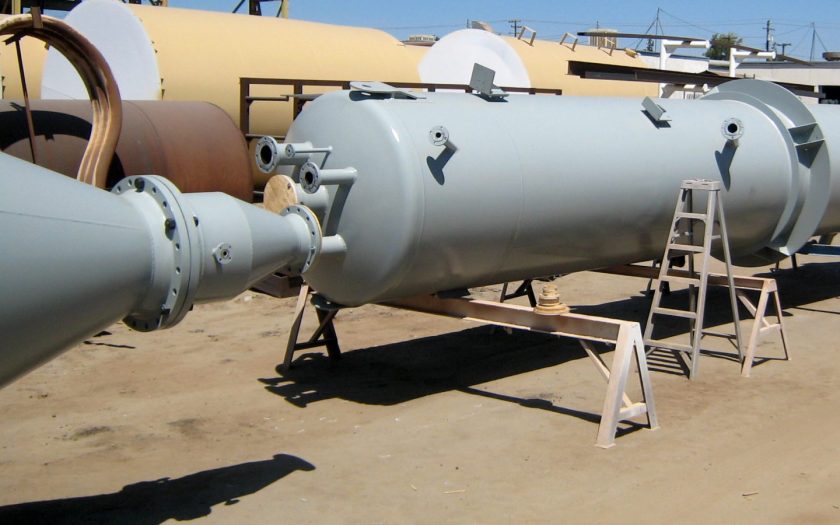
No, this has nothing to do with the movie “The Purge”! Sorry for the disappointment! However, I am going to write about an interesting topic here, that is if you are interested in bulk solids handling applications.
The chemical industry is one of the biggest users of bulk solids, which can include powders, pellets, resins, flakes, and other forms. In many chemical plants, these bulk solids are heated, cooled, transformed, dried, cured, reacted, or purged, at one or more points in their processing. This may involve passing a gas through a bed of particles. In such cases, often times an upward-flowing gas is introduced into a vessel (also called column, silo or bin) containing the bulk solid.
For example, in oil and gas industry, downstream activities can involve plastics manufacturing such as polyethylene or polypropylene resin. Such a manufacturing plant can have a purge column or a degasser vessel following the reactor. This purge column(s) can serve several purposes. It can reduce residual volatiles in plastics to an acceptable level using nitrogen or other inert gas. It can deactivate the trace catalyst residues by using a small quantity of steam. It can also provide surge capacity between the reaction and extrusion operations. Such gas introduction is also used in other applications/industries. For example, a conditioning vessel may add or remove moisture from a bed of a bulk material flowing downward by gravity using upward flowing air with controlled temperature and relative humidity.
Typically these purge columns have a tall cylinder section followed by a hopper section(s). Often, they may have internal/inserts inside. The operation of such vessels is based on gravity flow. If the vessel is not designed appropriately using scientific bulk solids flow principles, problems can occur that limit their effectiveness. Incomplete purging or non-uniform conditioning can be caused by localized fluidization, non-uniform gas distribution, and non-uniform solids velocity profiles and result in off-grade product, fire/explosion risks, environmental compliance issues, or downstream handling problems. Other problems include excess purge gas usage and product cross-contamination during grade changeovers.
The design of such vessels (or modification, if fixing problems with an existing vessel) should start by clearly defining process requirements. Understanding of the minimum and maximum purge duration (i.e., time of exposure to purge gas), required solids and gas flow rates, gas temperature and pressure at the top of the vessel is critical. Solid’s residence time in the vessel can be controlled if the flow pattern through the vessel is mass flow, which results in a first-in-first-out flow sequence. In order to design a mass flow processing vessel with gas injection, the flow properties of a material must be known. Important flow properties include cohesive strength, wall friction, range of bulk densities, and permeability.
Purge gas should be introduced just above the top of the conical hopper section using a proper method. Jenike & Johanson’s J-Purge™ technology has proven the test of time. This method of gas injection provides a uniform distribution of the purge gas, with no adverse effects on the flowing solids.
Following a proper design approach based on flow properties characterization and analysis of two-phase flow effects will ensure reliable purging, without any material flow consequences !