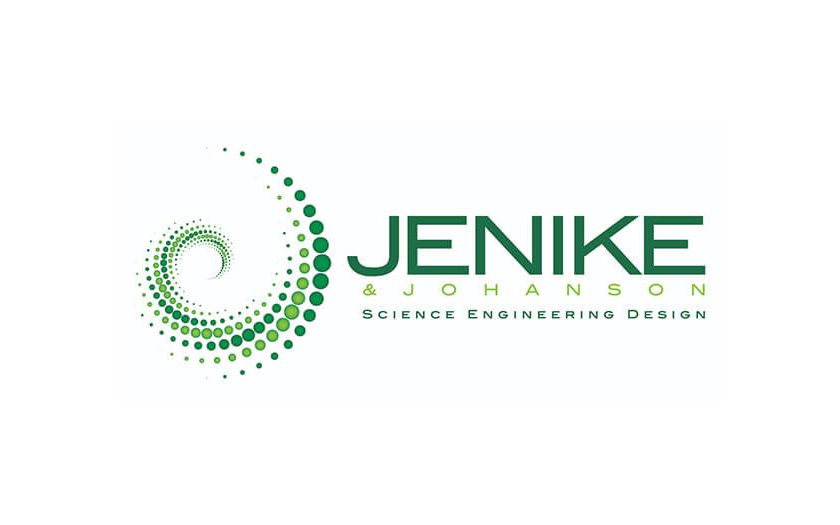
After handling a bulk solid for years, many believe that they know their material. They know which equipment works well and where in the system plugs are likely to occur. They know where to have the sledge-hammers ready, and where material flows without operator coercion. And sometimes, this experience leads to certain accepted truths about the material, which may not be true.
Recently, while reviewing a layout drawing, a couple of cyclones caught my eye. These cyclones were pushed up uncomfortably close against the roof-line of the plant, with no apparent reason. When I questioned, I was told that “at this plant, everything that’s sloping has to be at least 70°.” Based on this belief, the sloping pipes below the cyclones were made 70°, which resulted in the cyclones being up against the roof. In fact, they almost raised the roof to be able to fit the cyclones.
So what’s wrong with this picture? I’m not sure where the 70° angle edict came from. There is a minimum angle required for a chute to ensure material flow, but that angle is usually for a specific chute surface, as well as a specific impact pressure. It may have been possible to make the chutes less steep by selecting a lower friction surface. It is also generally possible to make chutes start at a steep angle, and as material velocity increases, decrease their slope. Using some of these techniques, it would have been possible to fit the cyclones in a much shorter headspace.
I have been in plants where all of the hoppers have the same slope; the angle that folks believe (based on their experience) is required to make a certain material flow. However, experience in this case can also lead us astray, since slope alone does not determine the flow pattern. The slope, in combination with the internal surface of a hopper determines the flow pattern. A low friction surface could provide [modal destination=”/your-need/poor-flow/hopper-flow-pattern-mass-flow/” link_text=”mass flow” caption=” ” caption=”Discharge pattern occurring in a silo, bin, bunker or hopper”] at a shallower angle, while a rougher surface would require a steeper angle. Ultimately, these design limits are not values easily determined by experience, but they can be quite easily obtain by material testing.
It is important to know your powder or bulk solids properties, but this requires more than observing the material in action. Often our experience shows us the equipment and the conditions under which a given material is hard to handle. When it comes to knowing the appropriate designs to achieve reliable handling, our experience provides us limited guidance. To really know our bulk materials, we must know certain key properties, such as cohesive strength during continuous flow and after storage time at rest, wall friction and chute angles against various surfaces with a range of surface roughness, compressibility and permeability. With these properties at hand, we can make reliable and sound design decisions that neither result in buildings being unnecessarily tall, nor systems that fail to produce at design rates.
Not sure which angle to take? Give us a call to discuss your options as our experts can help you make the right decision.