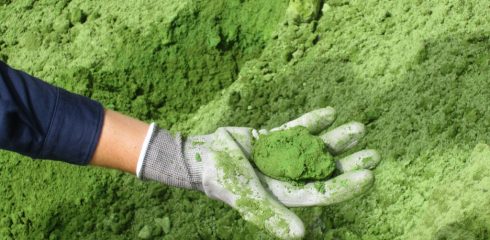
Overview
Glass & Ceramics Industry
Glass: We can help you improve the quality of your LCD screens, hand-held electronic displays, optical fibers, safety glass, light bulbs or beverage bottles.
Ceramics: Ceramics are commonly used to make abrasion resistant liners, insulation products (refractories), and filtering applications. If you are compacting your ceramic powders to achieve a higher density, we can help achieve consistent powder flow through your process.

Glass production process in an industrial setting.
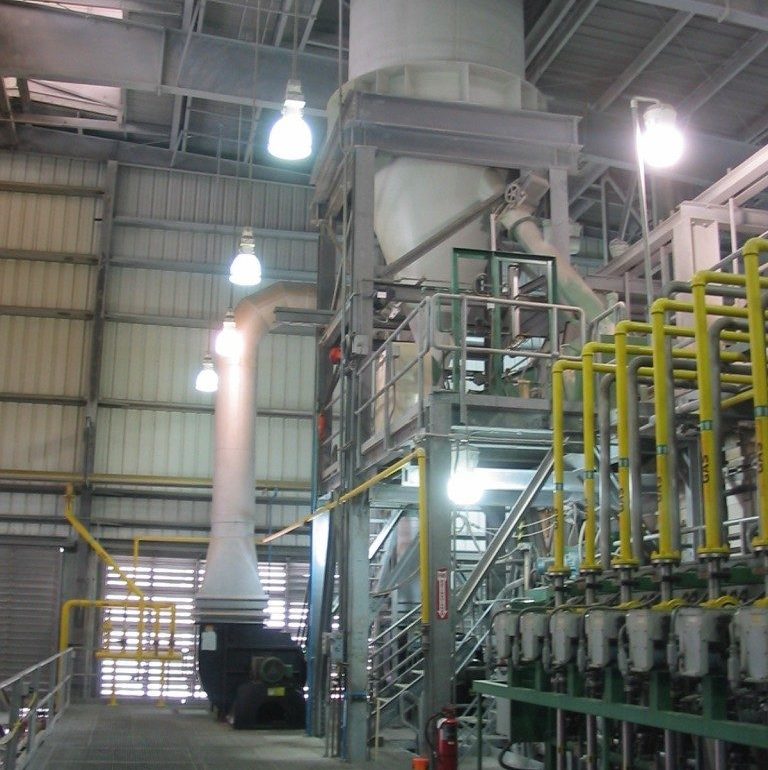