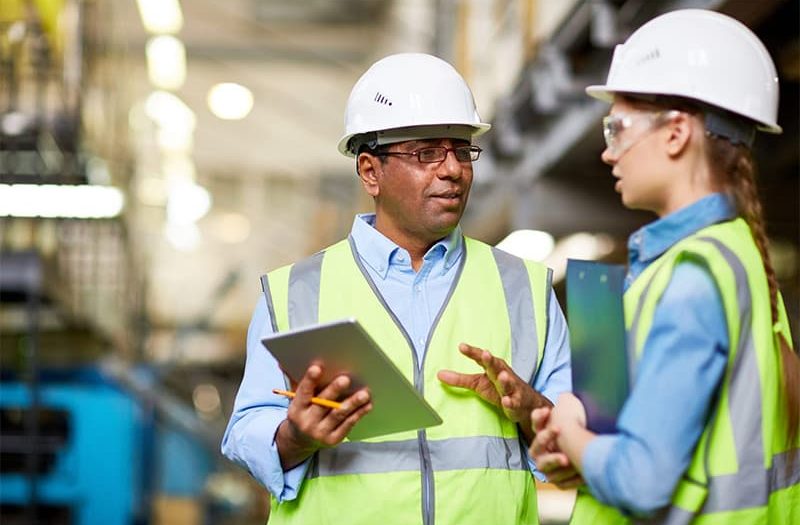
Powder flowability issues such as arching and ratholing can cause costly disruptions in silos, bins, or hoppers. Arching occurs when an obstruction forms above the outlet, stopping flow, while ratholing happens when only a central flow channel empties, leaving material stagnant. These issues lead to limited capacity, erratic flow, and equipment damage. Solutions include modifying equipment design and material handling processes to ensure consistent and reliable flow. However, each case is different and often requires experienced engineering support to diagnose and resolve critical issues.
Understanding Powder Flowability
Flowability refers to how easily a powder flows, which can significantly impact manufacturing and processing efficiency. Factors affecting flowability include particle size, shape, moisture content, and temperature. These factors must be considered during the effort to determine how powders behave under different conditions, influencing the design and operation of handling systems.
Approaches to Improving Powder Flowability
1. Material Testing and Characterization
Thorough material testing is essential to understanding the specific properties of the powder. Advanced testing facilities often conduct various tests, such as shear testing, wall friction testing, and compressibility testing, to gather data on powder behavior. These tests help predict how powders will behave in different conditions, informing the design of handling systems.
2. Flowability Analysis
Data from material tests are analyzed to determine the powder’s flow characteristics. Specialized tools and methodologies, like the Ring Shear Tester, help predict powder behavior and identify potential flow problems. These analyses provide a foundation for developing tailored solutions to improve flowability.
3. Customized Solutions for Equipment Design
Test data are used to design or modify equipment for optimal flow. Solutions might include custom-designed hoppers, bins, and feeders tailored to improve flowability based on the powder’s unique properties. Such equipment modifications ensure that powders are handled efficiently and consistently.
4. Surface Treatments and Additives
Surface treatments (such as applying anti-caking agents) and the use of flow aids (e.g., fumed silica, magnesium stearate) can enhance powder flow. Recommendations and implementations of these treatments are based on specific powder properties, ensuring the best possible outcome. These treatments help reduce inter-particle friction and prevent clogging.
5. Process Optimization
Optimizing the entire process, not just individual components, is crucial for improving powder flowability. Evaluations and redesigns of processes aim to minimize handling issues, reduce downtime, and improve overall efficiency. This holistic approach ensures that all aspects of powder handling work in harmony.
Best Practices for Ensuring Consistent Flowability
Flow problems are extremely common in industries handling powders. Many installations were designed and built with little consideration of the flow properties of bulk materials. A pertinent example is Northern States Power’s (NSP) coal-fired power plant in Minnesota, which was originally designed without the principles of flow analysis. Consequently, plant operators experienced flow issues with their bituminous coal. Read more about how the Jenike Shear Tester helped resolve critical safety issues at NSP while realizing greater storage efficiencies.
Beyond individual case studies, there are many best practices to bear in mind for maintaining and improving powder flowability:
- Regular Maintenance and Monitoring of Equipment: Routine checks and maintenance ensure equipment functions optimally and identify issues before they escalate.
- Evaluate the Impact(s) of Making Adjustments to Materials or Process Conditions: Ongoing evaluations and improvements may be essential as material properties and process conditions can change over time.
- Ensuring Comprehensive Material Testing and Analysis Before Implementing Solutions: Thorough testing and analysis provide the data to design effective handling systems and processes.
Closing Thoughts
Powder flowability is critical in efficient bulk material handling, impacting everything from product quality to operational costs. Leveraging the expertise of industry leaders and employing proven methodologies can lead to optimized processes and significant efficiency improvements.
For those facing challenges with powder flowability, consulting with experts in bulk material handling can provide cost-effective, tailored solutions and strategies. Our extensive experience and specialized knowledge can transform handling processes, ensuring a consistent and efficient flow of powders across various applications.