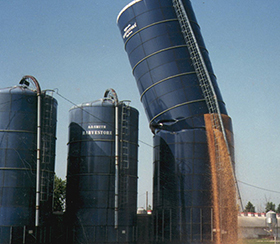
Bulk solids handling can be challenging. This is, in no small part, due to the interplay of material characteristics and dynamic flow behavior. The heterogeneity of particulate matter can lead to segregation, which could compromise end-product quality. Flow obstructions (arching, ratholing, etc.) can impede material discharge and operational continuity. Hygroscopic materials may cake and compact under varying conditions. There are numerous mechanisms, variables, and potential failure points that systems integrators need to consider to ensure seamless operation and economic viability of industrial solids handling systems.
Designing an optimal solids handling system is not easy, but it is a technical necessity. This blog will explore some of the most common design issues in solids handling systems. After you have completed this article, you will understand what to be wary of in relation to solids handling technologies and how to prevent issues that occur in solids handling systems.
Segregation of Blended Ingredients
Blended ingredient segregation is an extremely common design issue in solids handling systems. It occurs when different components of a blend separate during handling or storage, leading to inconsistent product quality. This problem is primarily due to differences in particle size, although shape, density, and surface composition may also come into play among the ingredients. For example, finer particles may accumulate near the center of a forming pile while the coarser particles roll to the periphery. Finer, lighter particles may stay airborne longer and accumulate at the top of a pile. Segregation can be exacerbated by vibration, air currents, and improper handling techniques. To mitigate this problem, it is crucial to design solids handling systems that minimize particle separation and maintain the integrity of the blend throughout the process.
Flow Interruptions and Limitations
Flow interruptions and limitations are significant challenges in solids handling systems. These issues within solids handling systems often arise from the improper design of storage vessels and handling equipment. Common solid flow problems in bins, silos, and hoppers include arching and ratholing. Arching occurs when the material forms a stable obstruction above the outlet, preventing further flow. Ratholing happens when stagnant material exists around the periphery of the storage vessel, and the bulk material preferentially flows through a narrow, central channel. As the channel empties, if the bulk material has sufficient cohesive strength, the rest may remain stagnant. Issues like these can lead to inconsistent flow rates and operational inefficiencies. It is essential to design storage vessels with proper geometries to address flow interruptions. Occasionally, given the right flow properties, flow aids, like vibrators or air cannons, can help under specific circumstances in material discharge.
Caking and Compaction
Caking and compaction are common issues in solids handling systems, particularly for hygroscopic materials, in other words, ones that absorb moisture. Caking refers to the formation of solid lumps within the material during storage or packaging. This can make discharging and handling difficult. Compaction occurs when the material is subjected to pressure over time, leading to densification and loss of flowability. Both issues can be exacerbated by environmental factors such as humidity and temperature changes. To prevent caking and compaction, it is important to understand the mechanisms that will trigger it and then control the storage environment. Sometimes, using anti-caking agents or mechanical agitation may be worthwhile to maintain material flowability.
Restricted Discharge Rates
Thanks to their flow properties, fine powders and cohesive materials often experience restricted discharge rates below the rates expected for the operation. To manage discharge rates, hoppers and feeders must be designed to accommodate the specific flow characteristics of the material. Techniques such as proper hopper angles and outlet sizing, controlled aeration, and, in certain situations, the use of vibration or flow aids can help achieve the required discharge rates.
Abrasiveness and Friability
Materials with abrasive properties can cause excessive wear on handling equipment, leading to maintenance issues and downtime. Friable materials, however, can break down into smaller particles during handling, generating dust and creating further handling challenges. Selecting appropriate materials for equipment construction and implementing wear-resistant linings can extend the lifespan of handling equipment. Additionally, dust collection systems should be designed to manage the specific properties of the material being processed. As a result, they can ensure a safe and clean working environment.
Dust Generation
Dust generation is common in solids handling systems and can pose health and safety risks. Effective dust collection systems are crucial for managing airborne particles and maintaining a safe working environment. Designing dust collection systems that cater to the material’s specific properties can significantly reduce dust-related problems. Proper equipment sealing, the use of dust collectors, and the implementation of dust suppression techniques are essential for effective dust management when using solids handling systems.
Looking for Design Assistance for Solids Handling Systems?
Addressing the common design issues in bulk handling systems requires a thorough understanding of material properties and the application of appropriate design principles. Engineers can design solids handling systems that operate reliably and efficiently by considering segregation, flow interruptions, caking, inventory control, and dust generation. Leveraging testing and engineering services, such as those provided by Jenike & Johanson, can help ensure optimal system performance and minimize operational challenges.
At Jenike & Johanson, we excel in diagnosing and addressing the complexities of solids handling systems. Utilizing our expertise of solids handling systems ensures optimized design and reliable operation, preventing common issues like segregation, flow interruptions, and dust generation. An often-heard statement by clients about a Jenike & Johanson-designed system: “It just works!”