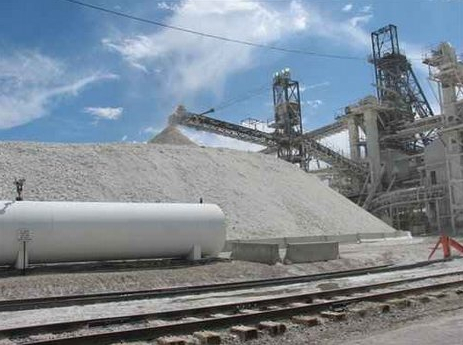
The Need
The world’s largest known source of natural sodium carbonate (trona) lies in the Green River formation in southwest Wyoming. FMC Wyoming is the largest of four companies operating in the region, which together mine roughly 15,000,000 metric tons of trona each year and produce over 8,000,000 metric tons of soda ash, which is roughly 80% of the soda ash produced worldwide from natural sodium carbonate.
The primary deposits in the Green River formation are found at depths of 400 to 3,500 feet in beds that range from 4 to 12 feet in thickness. Approximately 500 square miles of deposits contain high quality ore, but occasional pockets of insoluble impurities are common even in high quality ore deposits. When these unpredictable high levels of insoluble materials enter the process stream, it reduces yields and drives up production costs. To smooth out these variations in the ore FMC engineers needed to detect the troublesome ore, divert it from the process stream, and then meter it back into the process in a controlled way.
FMC found it could use an on-line analyzer to detect the level of insolubles in the ore as it moves on the conveyor belt from the mine face to the hoist. In order to segregate the high-insol ore and control its delivery, a large underground storage and handling system was needed, allowing operators to better control the flow of ore to the surface. With limited underground storage and miles of conveyors, matching the mine output to the hoisting capacity is a challenge. The additional storage would give the system a greater ability to adjust to surges from the mine face and maintain a constant flow of ore to the surface.
The Solution
Jenike & Johanson evaluated the feasibility of reliably handling the trona ore in two 1,300 ton capacity silos to be constructed underground. Flow properties tests on the trona confirmed what most operators knew: when stored at rest trona crystals grew together and formed a hard, solid mass. Surface moisture accelerated the process and resulted in higher strength. The tests provided the information necessary to design the silos for mass flow, which prevents stagnant, non-flowing regions where the trona could cake together.
Building two 25 foot diameter silos and a 200 foot conveyor system at a depth of 1,800 feet below the surface provided many challenges! Construction materials were evaluated for abrasive wear, loads were calculated on the structure and feeder, and a unique diverter was designed for the in-feed conveyor system.
The Result
Since startup in early 1998, the system has been operating reliably and has allowed the mine and processing plant to work together more efficiently and reduce production costs.