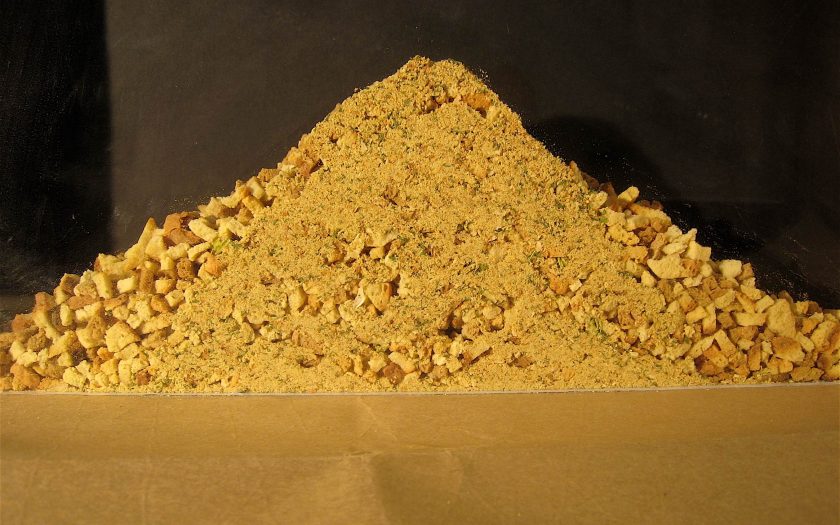
The Need
Most industries view segregation as a major problem. Particle segregation is prevalent in industries that handle free-flowing bulk solids containing a wide particle size distribution.
Kraft Foods (KF) produces Stove Top® Stuffing Mix. To meet increased consumer demand, KF installed a new handling system. During the start-up process, unacceptable variations in the particle size distribution of the bread crumbs occurred. It was imperative that the problem be quickly resolved, so that the high cost associated with unnecessary down time and wasted product could be minimized.
Jenike & Johanson’s on-site evaluation determined the problem was due to segregation in a new storage bin. For materials containing a wide range of particle sizes, such as the bread crumbs, sifting is the most prevalent segregation mechanism.
The flow pattern of the material through a bin will determine the severity of segregation in the discharged material. Observations made on site, and flow properties tests conducted by Jenike & Johanson, confirmed that the existing bread crumb bin was funnel flow. With funnel flow, the material flows primarily in a channel located above the discharge point.
Also, during discharge, fine particles can sift through the stationary coarse material, creating areas of high fines concentrations.
Since a funnel flow pattern results in a first-in, last-out sequence, material in the stagnant regions may remain there for an extended period if the bin is not routinely emptied. This becomes especially important when handling food products, where spoilage is a major concern.
The Solution
Jenike & Johanson quickly determined that the solution to this segregation problem was to convert the flow pattern from funnel flow to mass flow (the flow pattern where discharge of any material from the bin causes the entire contents to move). In such a bin, since the material moves down as a unit, if the fines and coarse segregate in a side-to-side pattern during filling, they are reunited at the outlet of the bin. In addition, there are no stagnant regions during discharge; therefore, the problem of spoilage is easily eliminated.
To maximize capacity, the existing bin had unfortunately been designed to be rectangular with a pyramidal converging section, which resulted in valleys that were 10º shallower than the adjacent hopper walls.
To provide mass flow and solve the segregation problem, three options were considered. The first option was to line or coat the hopper walls to provide a significantly less frictional surface – a suitable surface was unlikely to be found. The second option was to replace the existing bin with a new one, properly designed for mass flow – this would be costly in dollars and time. The third option was to modify the existing bin with one of our BINSERT® system. A BINSERT® design provides mass flow with the use of a smaller, steeper hopper placed inside an existing hopper. In this case, a pyramidal inner hopper would be required. Due to the extremely shallow valley angles, we also recommended valley plates for this design.
Another benefit of using the BINSERT® design is better control over the velocity profile in the hopper section. The BINSERT® is capable of maintaining a more uniform velocity profile throughout complete discharge of the bin.
The Result
KF installed our recommended inner pyramidal hopper and valley plates in the existing bread crumb bin. Since the installation, segregation has been noticeably reduced, the size distribution of discharged particles has been much more uniform, and, as a result, product quality has increased.