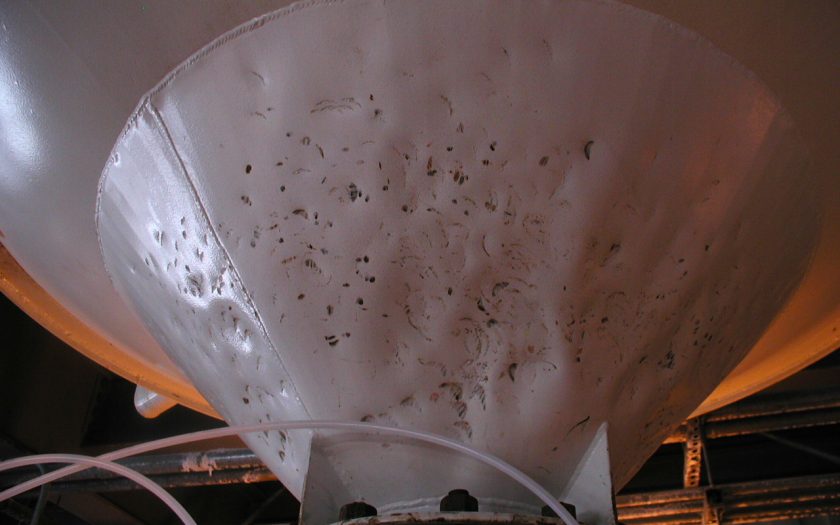
The Need
Owens-Brockway Glass Containers, a unit of Owens-Illinois, produces flint and green glass in three regenerative furnaces, each of which has four chargers. When the plant was built, an overhead monorail system was used to ferry mixed batch in 4,000 lb. cans from the batch house to the furnace feeders. This system was designed so that a series of four cans could be positioned over the chargers, with one can feeding each charger.
Operators had to constantly adjust the feed rate of each charger so that all four cans would empty at the same time. As production increased, it became more and more difficult to maintain a constant delivery of batch to the furnaces.
After the bins were installed, operators found that they could not use all of the new storage capacity because glass quality deteriorated when the bins were drawn down. Plant engineers determined that the problems were the result of changes in batch composition that could be traced to segregation in the batch storage bins. To avoid production problems, the bins had to be kept at least 50% full, and operators attempted to keep the bins topped off to maximize the available surge capacity.
Our observation of the top surface of the material in one of the bins revealed a fast, central flow channel typical of a funnel flow pattern. Inverted inserts, such as the one used in these bins, are often used to expand the flow channel in a bin in an effort to achieve more uniform flow. In this case, however, the insert was too small and placed too far from the outlet to be of any benefit.
The Solution
The proposed modifications had to meet several important criteria:
- Minimize segregated discharge of batch
- Fit within the space occupied by the existing conical hopper
- Accommodate occasional large lumps of cullet, paper, rags, etc.
- Be robust enough to withstand the highly abrasive glass batch
Jenike & Johanson recommended a BINSERT® hopper system because it offered excellent velocity control—a key element in eliminating problems due to sifting segregation—and allows a shallower outer hopper to be used.
We constructed and tested a quarter-scale model in our laboratory to verify the design. The model was tested with samples and a full scale model of the inlet chute and top of the bin was also tested to refine the design of the inlet distributor.
Based on field measurements and drawings of the existing equipment, we designed the new equipment as a combination of bolted and field welded assemblies that would allow easy field installation.
The Result
We provided a performance warranty, which guaranteed non-segregated discharge from the bins, as part of the equipment supply contract.