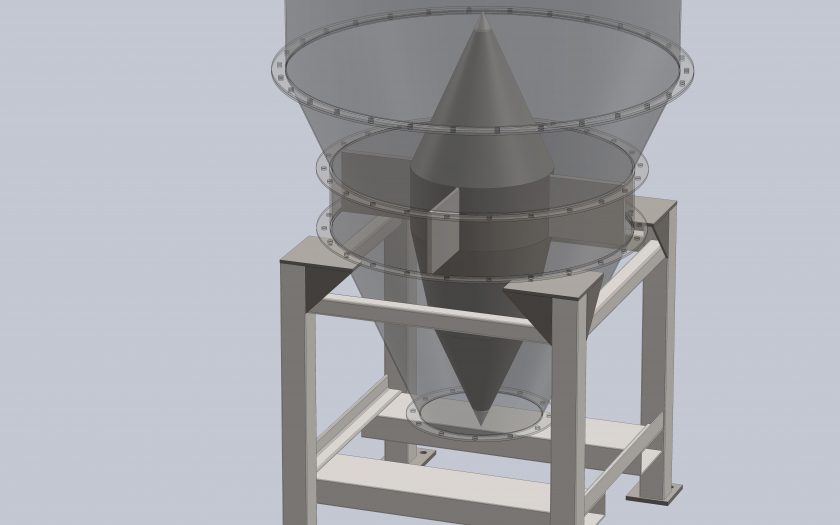
The Need
T. Anthony (“Tony”) Royal, a vice president with Jenike & Johanson, was named as a co-inventor on a patent for a unique pressure vessel and lock hopper system used to decaffeinate green coffee beans.
During the process, caffeine-free liquid carbon dioxide enters near the bottom of the vessel and flows in an upward direction, through a contact bed of stationary beans. The liquid becomes caffeine-laden and exits near the top of the vessel. Using lock hoppers, small batches of fresh beans are periodically introduced into the top of the 5,000 psi processing vessel, with an equal amount of decaffeinated beans withdrawn from the bottom.
It was critical that the new equipment would operate as intended, because its expected high cost would make future modifications economically unfeasible.
To process the green coffee beans economically, a relatively large capacity vessel was required. The vessel had to be operated at pressures of up to 5,000 psi to maintain the carbon dioxide in its liquid form.
For the process to be effective, the beans had to proceed through the vessel in a uniform pattern. The resulting first-in first-out flow pattern would achieve uniform residence times for each batch of material in the vessel. A minimum residence time was critical for proper decaffeination of the beans.
The size of the outlet was another concern. While a relatively large outlet would provide high discharge rates, the resulting large, high pressure valve would be expensive to purchase and maintain. Therefore, the valve had to be as small as possible, but still provide the maximum required discharge rates.
In addition to outlet size, the direction of fluid flow during discharge had to be considered. Beans had to discharge from the large pressure vessel to a smaller one.
As the beans filled the smaller vessel, the fluid occupying that vessel would be displaced. Without another exit, that fluid would have to leave the smaller vessel though the same opening as the beans were entering.
The Solution
Jenike & Johanson developed a cost-effective design that provided uniform mass flow and the required discharge rates. Mass flow was achieved by making the vessel’s hopper walls smooth and steep enough for the beans to flow along them. Laboratory tests were run to determine the wall angles required for mass flow and water was substituted for the liquid carbon dioxide
An insert was designed to be placed inside the conical hopper to ensure mass flow. This allowed the walls to be less steep and therefore minimize the overall height of the vessel— which reduced its capital cost.
Jenike and Johanson determined the proper outlet dimensions by using our proprietary two-phase flow computer program. In order to minimize the size of the outlet valve and its associated costs, we concluded that fluid flow had to be in the same direction as that of the discharged beans, and at a specified rate. By providing another exit for the fluid displaced from the lower lock hopper, this fluid could be injected into the larger vessel through a distributor located just above its outlet, thereby providing a flow co-current with that of the beans.
The Result
The laboratory testing, modeling work, and innovative J&J thinking provided a sound basis for the design of the pressure vessel. The equipment was installed and operated as expected. Initial costs were minimized, and no modifications were necessary. The design was unique and a patent was awarded, naming Tony as a co-inventor.