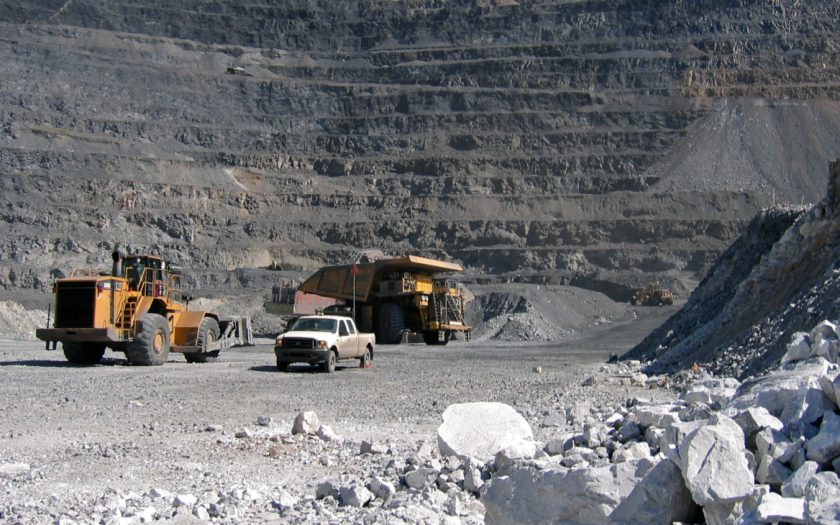
The Need
Demands for increased production from existing flash smelting furnaces have led to increased concentrate burner feed rates and the use of more finely ground concentrates. Unfortunately, feeding finer materials at higher rates increases the likelihood of erratic flow or even flooding from the furnace charge bin, usually located above the furnace. The safe and efficient operation of any flash smelting furnace depends on a continuous, non-pulsating feed of dry charge mix, at an accurately controlled rate. BHP Copper operated a 3,400 tons per day dry concentrate, single burner, Outokumpu flash smelting furnace at its San Manuel copper smelter in Arizona.
The Initial Problem
The first six months of furnace operation were plagued by serious flooding problems. The fine concentrate sometimes became aerated during discharge from the bin and flowed like a fluid at very high, uncontrollable rates to the burner. This resulted in upset conditions at the concentrate burner, leading to poor furnace metallurgy. Serious flooding problems also caused a large buildup in the waste heat boiler, which required a lengthy furnace shutdown for removal. The flow pattern in the dry charge bin was funnel flow, which occurs when a hopper is not sufficiently steep and smooth to force material to slide along the walls, or when the outlet of a bin is not fully effective, as is almost always the case when a drag chain is used as a feeder.
The New Problem
To increase the smelting capacity of the flash furnace, the capacity and reliability of the dry charge storage and feed system had to be increased. BHP defined the following performance criteria:
- 360 metric tons of live operating capacity in the storage bin;
- steady, uniform feed to the burner at a nominal rate of 220 dry metric tons per hour;
- minimized probability of flooding;
- minimized particle segregation effects;
- selection of feeders to reduce maintenance costs.
Fine powders may be handled by keeping them fluidized or by preventing fluidization and handling the solid in a contact bed. Powder flow properties and required feed consistency drive the choice. To achieve the required feed rate accuracy to the concentrate burner, the decision was made to use a mass flow bin with sufficient capacity to allow enough time for fluidized material to deaerate during storage before being discharged through the feeder.
We tested a number of concentrate-flux mixes to determine the flow properties to be used in designing a suitable mass flow bin. Tests run with a Jenike Shear Tester showed that the minimum outlet dimension required to prevent formation of an arch in a wedge shaped mass flow hopper was only 0.1 ft., even after 3 days storage at rest. Thus, the bin outlet dimensions were set by flow rate considerations.
Wall friction angles were determined on several surfaces, but 2B finish, stainless steel sheet was found to be the best hopper lining material, requiring the least steep hopper slopes for mass flow and, thereby, maximizing storage capacity within the limited amount of available headroom.
A bin outlet must be large enough to achieve the required discharge rate. The maximum flow rate of a fine powder through the outlet of a mass flow bin is low compared with that of a coarse, granular solid. Permeability values are used to calculate critical, steady-state discharge rates from mass flow hoppers, as well as the time required for fine powders to deaerate and settle in bins. The copper concentrate-flux mix has a very low permeability, so we performed a two-phase gas-solids analysis to ensure that material would flow from the bin in a steady flow mode. The maximum flow rate calculated was 350 dry metric tons per hour, which is considerably higher than that required by BHP.
The Solution
The Initial Solution
In a [popover image=”/your-need/poor-flow/hopper-flow-pattern-mass-flow/” link_text=”mass flow” title=” ” content=”Discharge pattern occurring in silo, bin, bunker, or hopper” direction=”right”] bin, all the solids flow without stagnant regions, whenever any solids are withdrawn. Advantages of mass flow bins include: uniform flow, feed density independent of the head of solids in the bin, a first-in-first-out flow sequence, ensuring uniform residence time and increased time available for deaeration; and minimization of segregation effects.
When major flooding problems first occurred, there was no time to convert the bin to mass flow. To get the furnace back into operation quickly, Jenike & Johanson recommended a tapered interface piece be fitted between the hopper outlet and the drag chain. This dramatically improved bin operation by creating a much larger flow channel. Maintaining bin contents at between 320 tons and 550 tons eliminated flooding and achieved reasonably smooth feed to the burner. Operations continued in this mode for the next 10 years.
The New Solution
Jenike & Johanson recommended removing the existing pant-leg hopper arrangement, installing four mass flow hoppers, and lining all interior sloping surfaces with stainless steel sheet with a 2B surface finish. This design provides a bin with 370 metric tons of effective live capacity. A minimum level of 110 tons of material in the bin was set, providing a 30-minute minimum retention time for deaeration (110/220 tph).
To achieve a uniform velocity profile in the new mass flow bin, we evaluated the use of STAMET (Posimetric feeder) multi-disc feeders coupled with air slides. STAMET feeders utilize an innovative design with a single moving part that provides evenly metered output across the full width of the outlet. This unique design allows easy metering and feeding of a wide range of materials, including fine powders, at low to very high rates. The feeders are extremely rugged and experience very little wear, even with abrasive materials.
Because this type of feeder was new to the copper industry, we constructed a 1/6th scale model of a ¼ section of the bin. The tests verified that the STAMET feeder produced a mass flow pattern with a uniform velocity profile in the bin. Flow from the discharge of the air slide was steady, without pulsations. The test rig was run at rates as high as 80kg/min., which, for the full-size facility, is equivalent to more than three times the design requirement. The tests demonstrated that the combination of a mass flow bin, STAMET feeder, and air slide is a robust system suitable for feeding the hot furnace charge at high rates to the concentrate burner.
The structural and mechanical design engineering for the modification was performed by H.G. Engineering. The multi-disc feeders were supplied by Carlingview Technologies, Ltd., under license to STAMET, Inc. Construction management for the project was undertaken by Fluor Daniel.
The Result
The pilot-scale modeling work proved the concept of discharging and feeding the fine, abrasive concentrate with an innovative material handling solution.