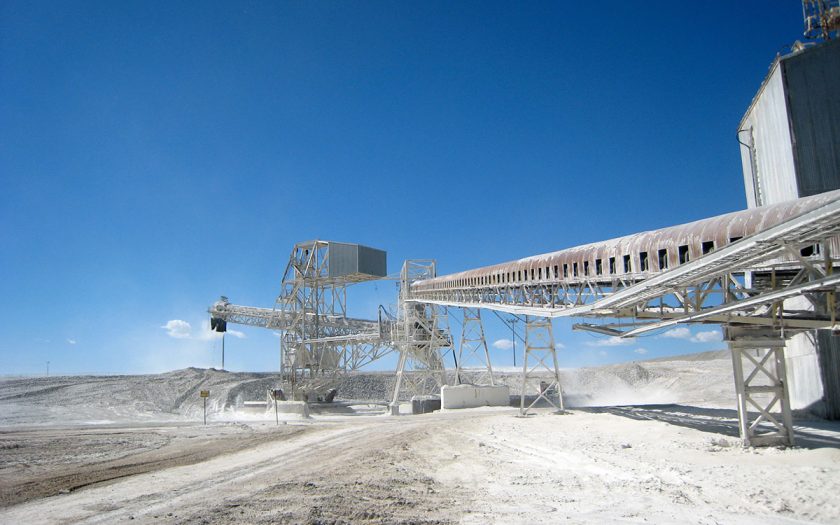
The Need
One of our clients had a problem of packaging different grades of kaolin clay uniformly into bulk bags at high rates. The clay’s poor handling characteristics made it very difficult to maintain uniform discharge from the 100 ton silos to the packaging equipment. Discharging from the silos at a high bulk density was also critical for stable bulk bags and efficient packaging.
Our testing revealed that the existing silos discharged the kaolin clay in a [popover image=”/your-need/poor-flow/hopper-flow-pattern-funnel-flow-cohesive-material/” link_text=”funnel flow” title=” ” content=”Discharge pattern occurring in silo, bin, bunker, or hopper” direction=”right”] pattern. With the poor flow characteristics of the material, this can result in stable arches and ratholes.
Additional problems with this funnel flow discharge pattern included erratic flow and reduced live silo capacity. As a fine powder, kaolin clay can become aerated and behave like a fluid, flooding through downstream equipment if a rathole collapses or fresh material is added to the silo.
The Solution
The design had to meet the client’s three primary needs:
- Each silo must have a 100 ton “live” capacity
- Discharging clay must have as high a bulk density as possible
- Silos must discharge the clay at a minimum rate of 6 tons per hour
Our first step in the solution was to design silos that ensured [popover image=”/your-need/poor-flow/hopper-flow-pattern-mass-flow/” link_text=”mass flow” title=” ” content=”Discharge pattern occurring in silo, bin, bunker, or hopper” direction=”right”]. To overcome the arching capability and frictional characteristics of the clay, we selected a transition hopper (designed with a long slotted outlet instead of the round outlet of a typical conical hopper). This design allowed us to create less steep wall angles than in a cone, thereby saving headroom. It was also easier to mate a feeder to the slotted outlet, which would be sized to prevent arching.
The next challenge was to achieve the desired discharge rate. Kaolin clay’s low permeability was highly rate limited in gravity flow. The usual solution for increasing flow rates in fine materials—aerating them to create a fluid condition—was not appropriate for this application.
We recommended a custom-designed, oval-shaped, air-assisted discharger. Instead of aerating a large volume of material, the air-assisted discharger fluidizes only a thin layer of material near its walls. This thin layer of fluidized material greatly reduces friction at the walls, allowing material to flow along relatively shallow wall angles. Also, the addition of air overcomes the limiting rate problems and increases the packaged density in comparison to a fluidized system.
Scale model tests on the conceptual design confirmed the counter-intuitive notion that the addition of air would increase packaging density. We then designed, fabricated, tested, and supplied a full scale discharger.
The Result
Jenike & Johanson’s mass flow design met and even exceeded our client’s original requirements. It is not only an efficient and successful solution to a troublesome flow problem, but also very cost effective. Our equipment solution was one-third the cost of a comparable mechanical feeding technique.
In addition, our design was able to fill a one ton bulk bag in about two minutes—five times faster than the original requirement.