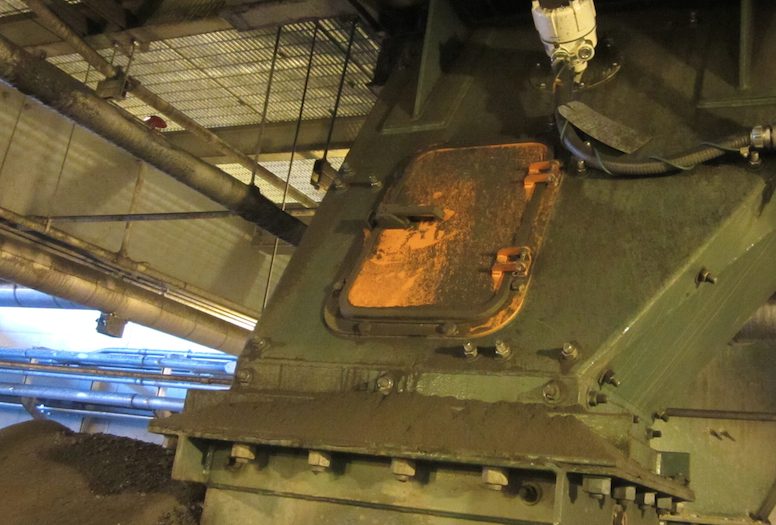
A leading power generation company operating a 600 MW coal-fired power plant recently started using coal that contained more moisture and fines than what the plant was originally designed to handle. The plant had a system of belt conveyors that transferred coal from the yard to the fuel silos. There were some transfer points in this system where conveying was switched from one belt to another. This fine and moist coal began to cause major flow problems in the conveying system, which had tall drops and sudden changes in direction. Transfer points within the system would not always reliably move the material. Coal would build up in the chutes, decreasing the cross-sectional area and eventually plugging the chutes completely. Plant operators would have to clear the chutes, which meant that not only was the plant experiencing increased downtime, but the employees had to leave their tasks to restart the flow
The Solution
Jenike & Johanson (J&J) was hired to perform flow property testing to determine the coal’s flow behavior based on its moisture content. Using this information, J&J was able to use Discrete Element Modeling (DEM) analysis to determine the source of flow problems in the power generation company’s transfer chutes as well as modifications needed to address the problems. The DEM simulation of the material flow confirmed that the drops and tight turns were responsible for the system’s unreliability. J&J then proposed a new configuration, working within the confines of the original system that would restore proper flow through smaller impact angles and consistent contact between the coal and the equipment.
The Result
Since the chutes were modified to handle coal that contained more fines and moisture, there has been no plugging or buildup at transfer points. J&J’s suggested design has allowed the system to operate reliably.