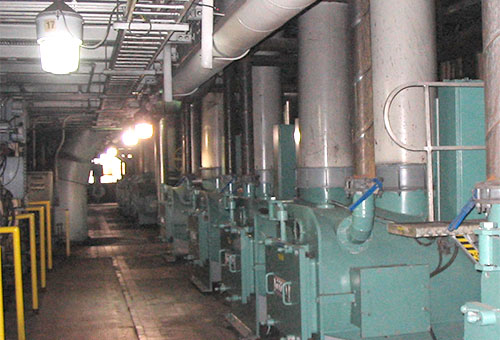
Standpipes are included as a feature in most power plant solid fuel feed systems, and yet their function is often not well understood. We have encountered many situations where the original design basis was sufficient, but a change in fuel was made that resulted in flow problems at the standpipe inlet.
To prevent the backward flow of hot gas from a downstream pulverizer or boiler feed system at a power plant, cool inert gas is added to the feeder housing. To be effective, this sealing gas must be at a slightly higher pressure than the downstream system. This results in an upward gas pressure gradient (pressure drop per unit length) that causes gas to flow counter to the fuel discharging from the bunker or silo hopper outlet. If not accounted for, this situation can result in erratic behavior or a stoppage of fuel flow entirely.
The feature typically included in the plant design to address this challenge is a standpipe, which is simply a vertical cylinder mounted between the hopper outlet and the feeder inlet. Its major advantage over other sealing methods is simplicity (no moving parts) and relatively low cost. However, to be effective in minimizing gas loss and preventing fuel flow problems, a minimum height is required (for a given diameter), which can be a problem if not accounted for during plant design. Often, “rules of thumb” are applied to set this height, which may or may not work depending on the situation. The fuel flow behavior can be assessed through the measurement of its properties — cohesive strength, permeability, compressibility and wall friction. With these properties in hand and the operating parameters known, the system can be modeled to determine the resulting gas pressure gradient at the hopper outlet. The impact of this gas pressure gradient on the potential for cohesive arching can be evaluated, and the gas leakage rate calculated. Thus, the standpipe height can be set during the design process to ensure that cohesive arching is prevented, and the expected leakage can be factored into the gas supply system.
If problems are encountered once a plant is built and in operation, particularly due to a change in fuel, all is not lost. Changes to the standpipe and feeder configuration, as well as the hopper design (shape and slopes, liner, outlet, etc.) can reduce if not eliminate the problem. Often, the investment in these equipment changes can be justified by the savings in fuel cost and plant downtime, so an engineering evaluation as part of an economic analysis is worthwhile.
Let us know if you’d like a consultation about any issues you’re experiencing at your facility.