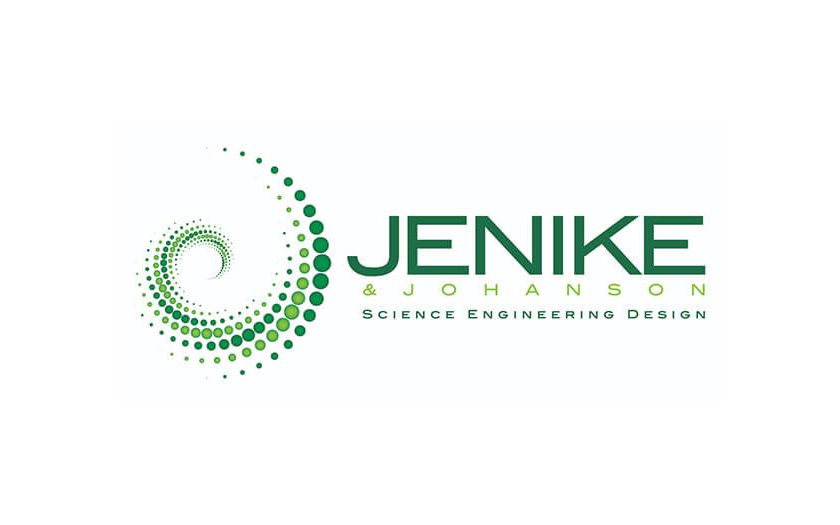
The number one rule of powder handling is that there are exceptions to every rule! Consider wall friction. In order to achieve mass flow and prevent ratholing, the walls of a hopper must be steep enough and low enough in friction to allow flow of powder along the walls. Therefore, smoother is better, right? Not necessarily! Wall friction depends on both the roughness of the wall surface and the physical properties of the powder. Particles that are pliable will have more contact with a wall surface than those that are rigid. A smooth surface may therefore have greater wall friction!
A powder having a significant number of fines is usually more cohesive. However, adding a small amount of a finer material, such as fumed or precipitated silica, may dramatically reduce the cohesive strength of the powder. Submicron particles act as spacers that reduce the attractive forces between adjacent powder particles. The addition of fines can actually improve flowability!
Fine powders or bulk materials that contain significant fines often exhibit a rate limitation when discharged from a hopper, bin, or silo. Because of a vacuum that naturally develops above the outlet when the voids in fine powders expand as the material discharges, the resulting counter flow of gas will hinder the solids flow. A solution to the problem of counter flow of air into the hopper is to add additional air to the hopper! By introducing a small amount of gas at the proper location above the hopper outlet, the vacuum is decreased, thereby reducing the counter flow of gas into the outlet.
To solve flow problems, shear cell and permeability tests should be conducted. Shear cell tests measure cohesive strength, which is used to calculate outlet diameters to prevent obstructions to flow, and wall friction, which allows calculation of mass flow hopper angles. Permeability testing allows steady-state discharge rates to be calculated and air injection systems to be designed.