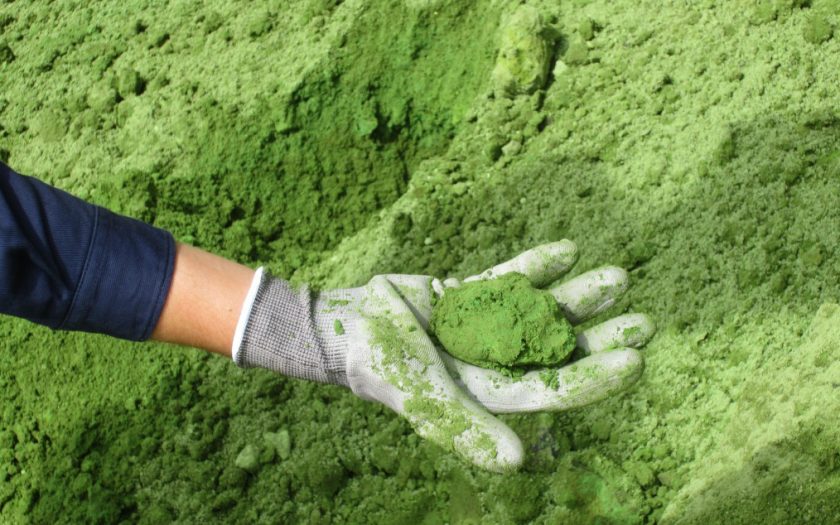
Powder caking, the undesirable agglomeration of particles into solid lumps or masses, poses significant challenges across various industries, including pharmaceuticals, food production, and chemicals. Understanding the underlying causes of powder caking is essential for developing effective prevention strategies. This article delves into the properties of powders and the environmental conditions that contribute to powder caking, drawing on insights from industry experts at Jenike & Johanson.
Intrinsic Properties Contributing to Powder Caking
Particle Size, Size Distribution, and Shape
Powder caking is significantly influenced by particle size, size distribution, and shape. Smaller particles, with their higher surface area-to-volume ratio, exhibit increased van der Waals forces and capillary condensation, which promote caking. A wide particle size distribution can lead to a denser packing structure, increasing interparticle forces and thus the tendency to cake, while uniformly sized particles tend to be less likely to cake. Additionally, irregularly shaped particles have a higher potential for mechanical interlocking, which can enhance powder caking. Spherical particles are less prone to caking due to fewer contact points.
Moisture Content and Migration
Moisture content and migration play crucial roles in powder caking. High moisture content increases the likelihood of liquid bridges forming between particles, enhancing cohesion and promoting caking. This is particularly pronounced in hygroscopic materials, which readily absorb moisture from the environment. Moisture migration, driven by humidity gradients or temperature fluctuations, can lead to localized condensation within the powder bed. This redistribution of moisture can create wet spots that act as nuclei for caking. Over time, these areas can expand, leading to a more extensive caked mass. Therefore, controlling moisture content and preventing moisture migration are essential for minimizing powder caking.
Chemical Composition and Impurities
The presence of certain chemical components and impurities can influence powder caking. Some materials may undergo chemical reactions, such as hydration or oxidation, that promote the formation of solid bridges between particles. Additionally, impurities can alter the surface properties of particles, affecting their interaction.
Particle Hardness and Surface Chemistry
The hardness and surface chemistry of particles determine their tendency to deform and adhere under pressure. Softer particles are more likely to deform and create contact points that facilitate caking. Surface chemistry, including the presence of surfactants or coatings, can modify the adhesive properties of particles.
Environmental Conditions Influencing Powder Caking
Temperature Variations
Temperature fluctuations, whether random or cyclic, significantly impact powder caking. In particular, wide temperature gradients during storage or transportation can induce moisture migration, where moisture moves from warmer to cooler regions within a bulk material. This migration can result in localized areas of high moisture content, promoting caking.
Storage at Rest
Extended periods of storage without movement can lead to particle consolidation and the development of powder caking. When powders remain static, the particles compact under their weight. This increases the size and number of contact points and potential for solid bridge formation.
Consolidating Pressure
The pressure exerted on powders during storage or handling can influence caking. High pressures can deform particles and increase their contact area, enhancing the likelihood of caking. This is particularly relevant in scenarios involving bulk storage in silos or hoppers.
Relative Humidity
The ambient relative humidity directly affects the moisture content of hygroscopic materials. High humidity levels can lead to moisture absorption by the powder, while low humidity levels can result in desorption. Both processes can alter the cohesive forces between particles, affecting their tendency to cake.
Testing and Mitigation Strategies
To address powder caking, it is essential to conduct comprehensive testing under representative environmental conditions. Key tests include:
- Direct Shear Strength Testing: Evaluates the effects of pressure, temperature, moisture, and time at rest on powder cohesion.
- Moisture Sorption/Desorption Analysis: Assesses the hygroscopic behavior of powders and their tendency to absorb or release moisture.
- Morphological Examination: Uses microscopy to observe particle shape and size, aiding in the identification of factors contributing to caking.
- Surface Energy Measurement: Characterizes the surface properties of powders, providing insights into their adhesive behavior.
Mitigation strategies may involve modifying storage vessel designs, controlling temperature and humidity conditions, and using anti-caking agents to reduce particle cohesion. By understanding the intrinsic properties and environmental factors influencing powder caking, industries can implement effective measures to prevent this common problem.
We want to help you overcome any challenges you may experience with caked powder. For more detailed information on our powder caking and testing services, contact us today.