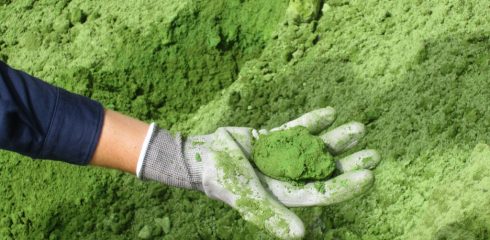
What is Poor Flow?
Two costly flow problems experienced in a silo, bin, or hopper are arching and ratholing.
Arching (bridging) occurs when an arch-shaped obstruction forms above the hopper outlet and stops flow. It can be an interlocking arch, where large particles mechanically interlock to form an obstruction, or a cohesive arch. A cohesive arch occurs when particles bond together due to effects of moisture, fines concentration, particle shape, temperature, etc.
Ratholing occurs when discharge takes place only in a flow channel located above the outlet. If the material being handled is cohesive, the material outside of this channel will not flow into it and may cake or agglomerate. Once the central flow channel has emptied, all flow from the silo stops.
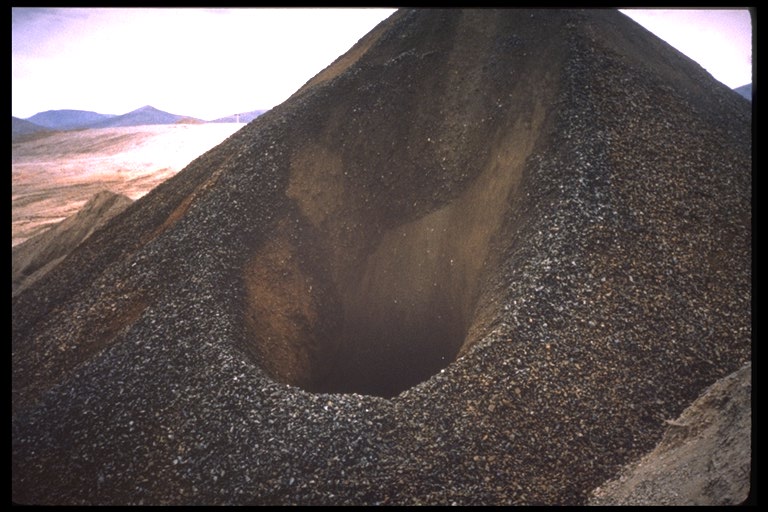
A rathole has formed in a stockpile.
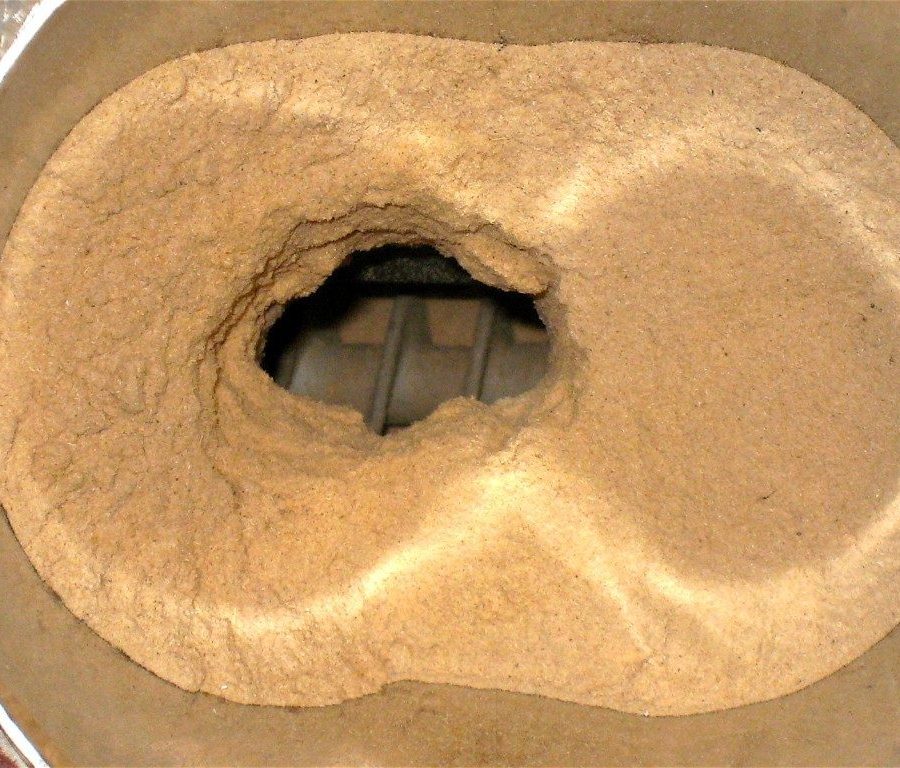
A rathole within a hopper that for sawdust.
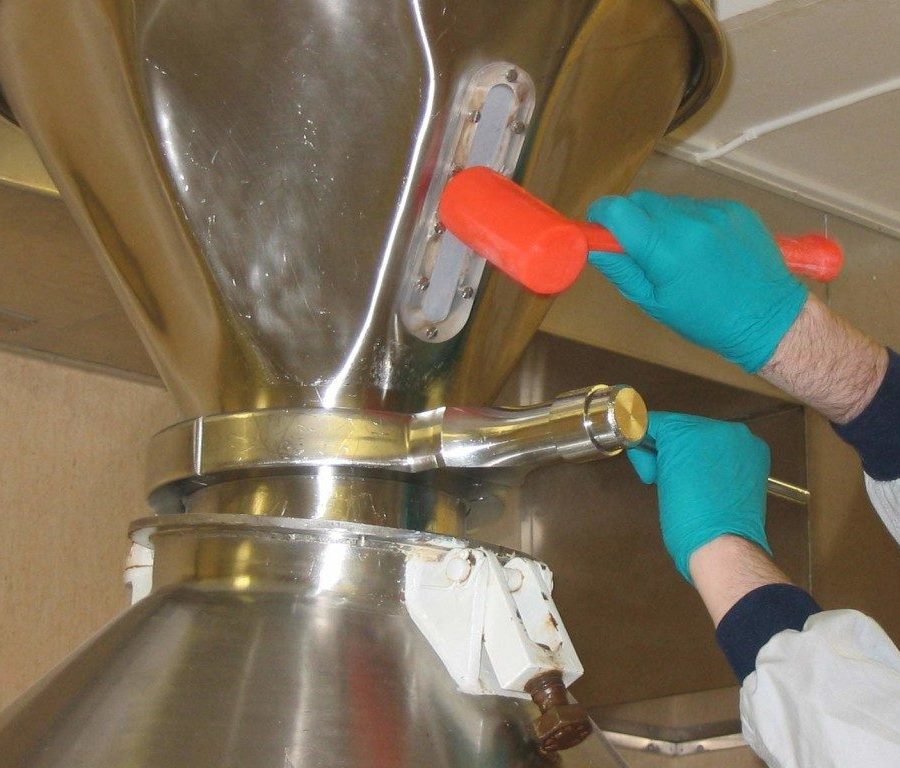
A hammer is used in an attempt to get built-up material within a hopper to flow again.
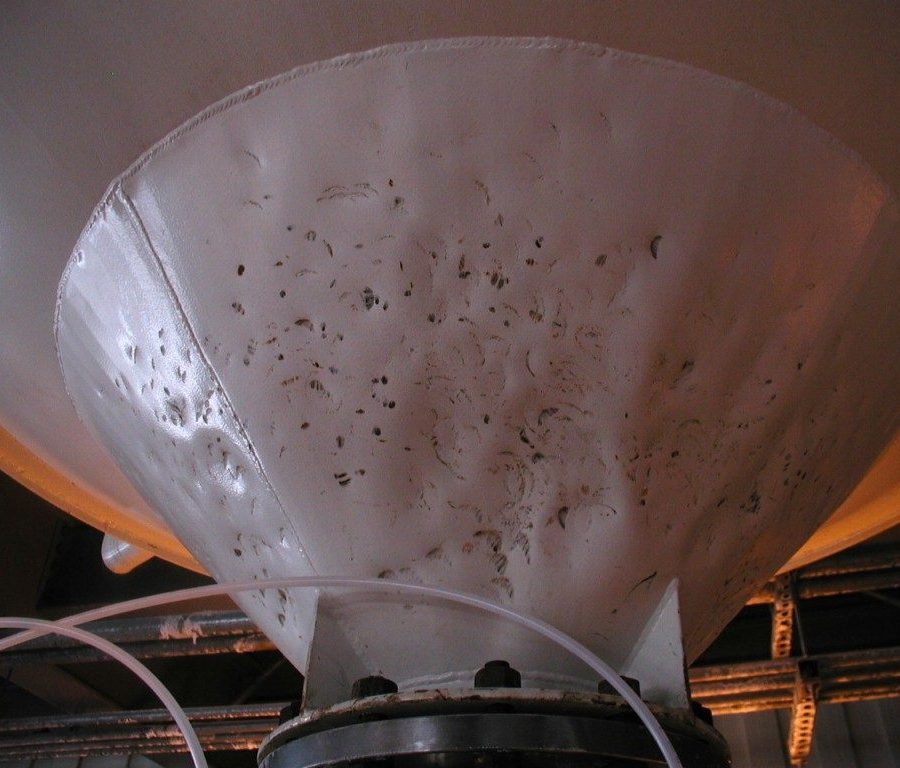
Damage from using a hammer on this vessel. Commonly called "bin rash".
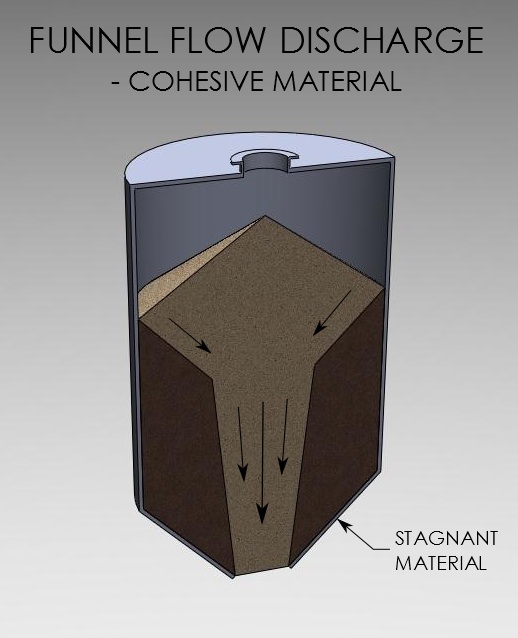
Funnel flow is a flow pattern in which solids flow in a channel formed within stagnant material.
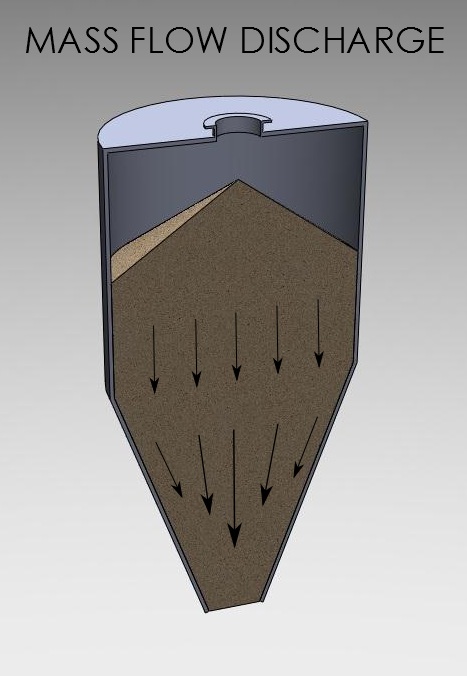
Mass flow is a flow pattern in which all solid in a bin is in motion whenever any of it is withdrawn.
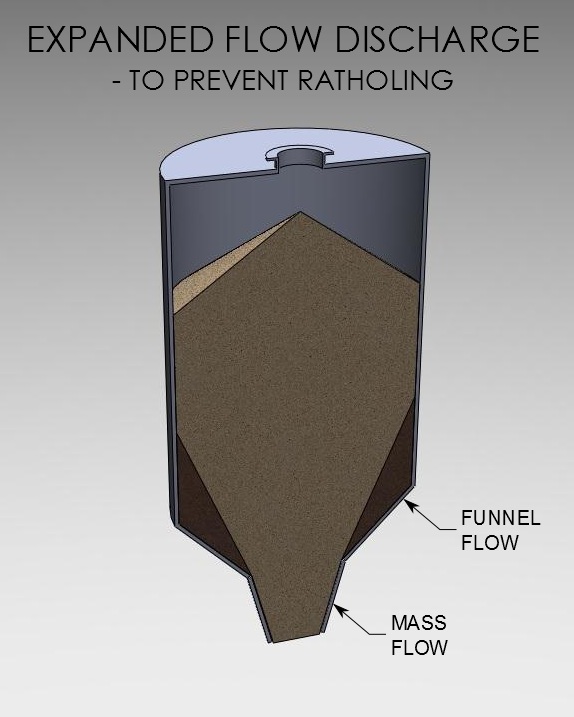
Expanded flow discharge can be used to prevent ratholing.