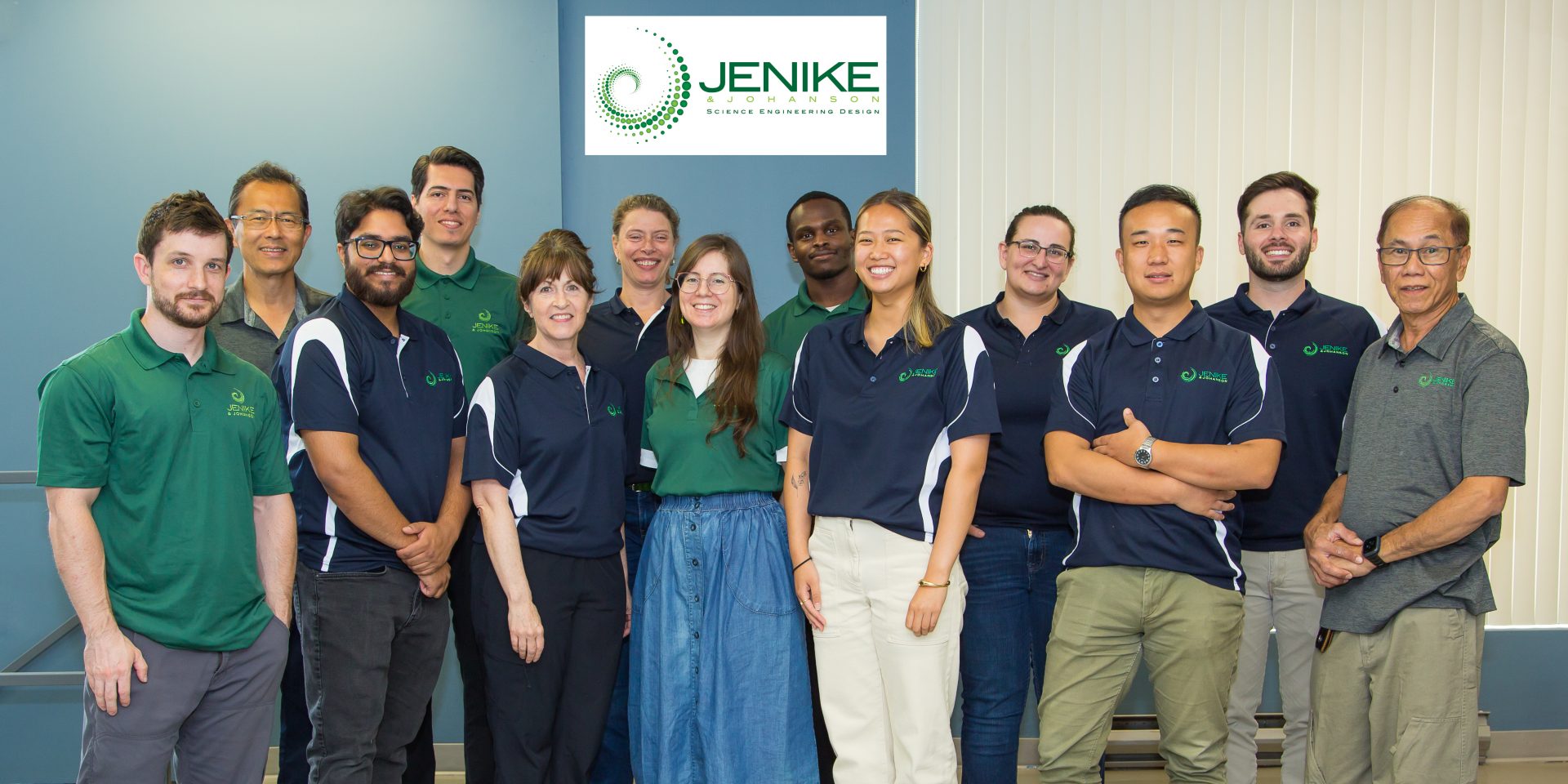
Overview
Processing Vessels Overview
Besides ordinary storage of bulk solids, silos can also act as processing vessels in which materials are dried, purged of VOCs, heated, cooled, cured, conditioned, or tempered. To facilitate processing, the vessels are equipped with heat exchangers or are modified to permit gas and/or steam injection. Examples of processing vessels for bulk solids include:
- Purge columns for polyolefins
- Conditioning of food products (e.g., sugar, wheat)
- Hopper dryers for reducing moisture of biomass or plastics
- Contact bed reactors (e.g., catalyst regeneration, reducing operations for DRI)
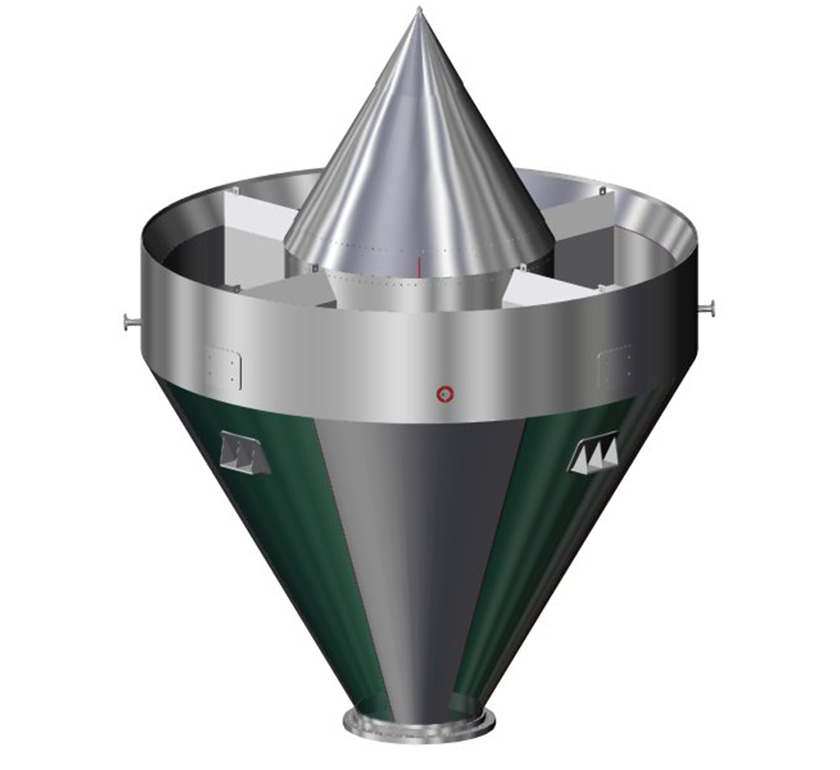
Conditioning silo internals.
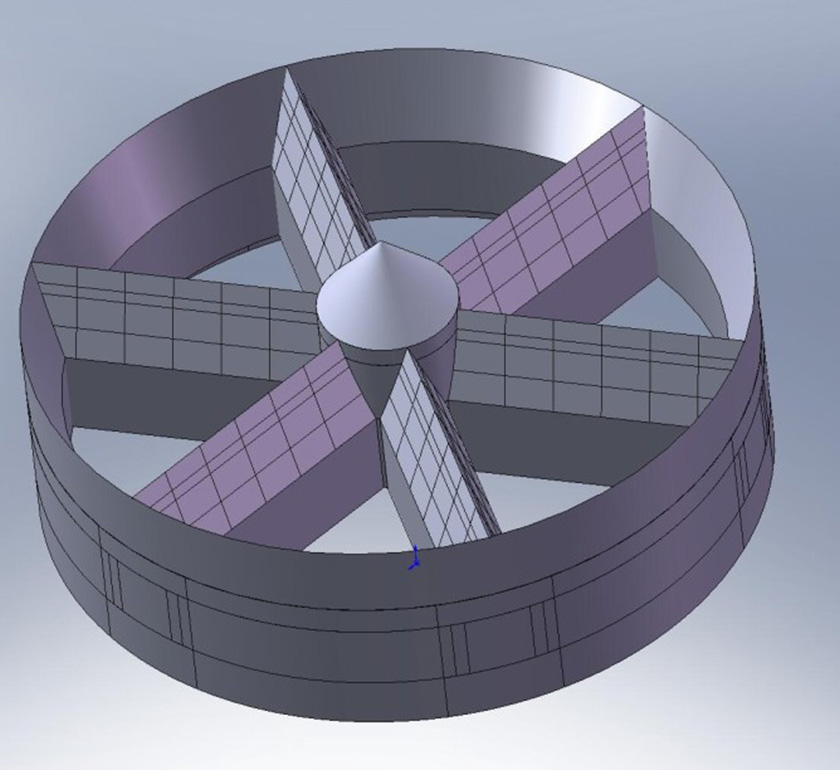
J-Purge system
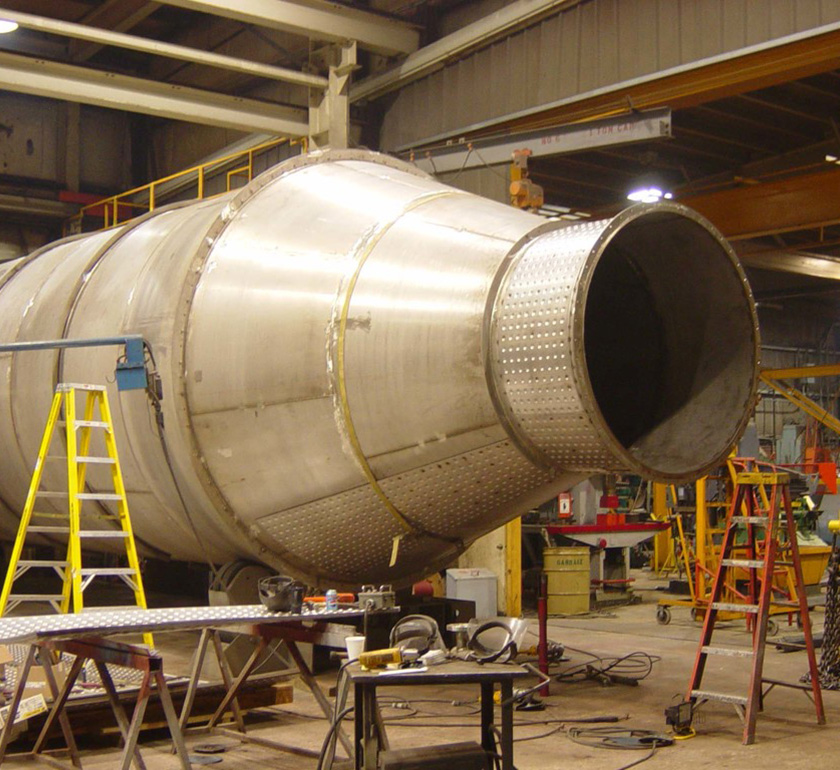
Silo cone fabrication