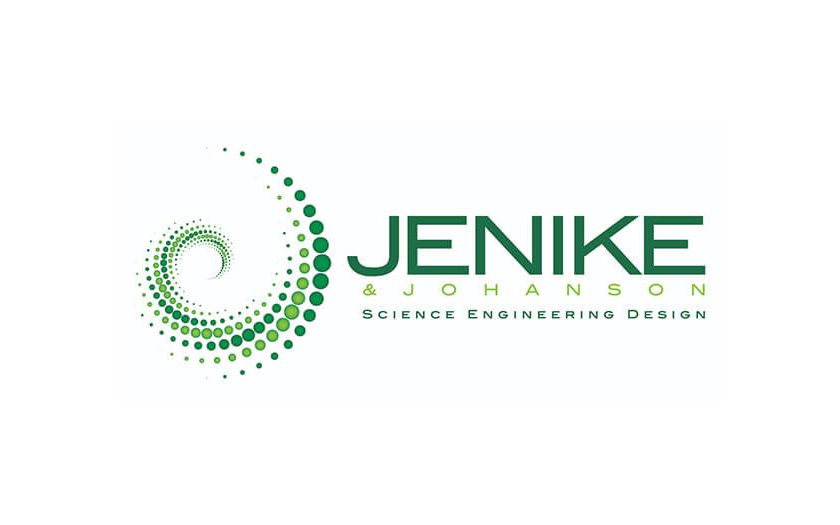
I am currently working for a variety of customers, and I have come to realize the experience we have can be very different, depending on the application. Often we are asked to develop a solution to an on-going material handling problem. The problem may be rooted in the design of the lower portion of a feed hopper, a larger storage bin or silo, and/or the equipment downstream, including feeders, valves, chutes, conveyors, etc. We gain insight to the problem from material testing, which gives us critical handling properties and the design limits for equipment features. This makes for an excellent resource, but here is where the challenge begins: what do we do with this information?
The situations we encounter typically have limitations that must be factored in, including space constraints, the time available for implementation and relative expense. We work in a wide variety of industries, and an approach that works in one may simply not be practical or possible in another. Here is where our experience can play a crucial role. We know that some industries cannot accept a wide variety of potentially contaminating materials, such as liners and coatings. In addition, some types of equipment are generally not practical in some industries. For instance, the pharmaceutical industry relies almost exclusively on round outlets for mating with butterfly valves and tube sections, while flow-promoting inserts (with hard-to-reach undersides) are generally not acceptable unless they can be removed by hand for cleaning. In contrast, the glass industry requires solutions that are wear resistant, due to the long duration of furnace campaigns (and the difficulty of servicing equipment once started), while some segments must avoid stainless steel due to the potential for chromium contamination. Finally, a roofing shingle manufacturer has concerns with the abrasive nature of granules leading to leakage and cross-contamination of operating equipment (valves and gates), while at the same time minimizing segregation due to stagnant material. These requirements can lead to vastly different solutions for otherwise similar problems that arise in these different industries.
I appreciate having the needed experience to work on a variety of applications, both personally and as a resource from others at Jenike & Johanson, and I look forward to the continued challenge of solving material handling problems faced by our customers.