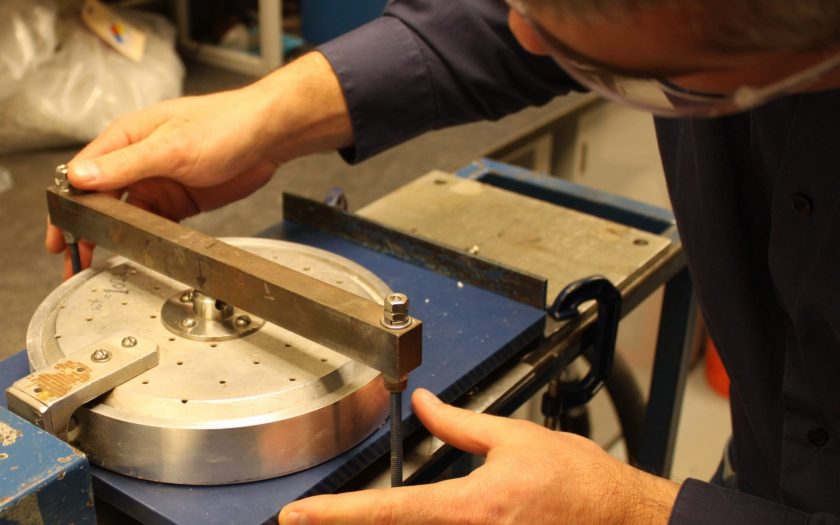
Powder flowability is a key property in a range of industries. It determines the ease with which powders and bulk solids flow through a system, which is influenced by factors as varied as particle size, shape, temperature, moisture content, and storage time at rest. Consequently, powder flow underlines both manufacturing efficiency and product quality. Testing flowability is, thus, essential for predicting material behavior during processing, storage, and transport. These tests contribute enormously to process optimization and quality control, helping to prevent issues like blockages, segregation, and inconsistent flow rates.
This blog post will explore some of the critical properties to assess in flowability tests.
1. Cohesive Strength
Cohesive strength measures the degree to which particles adhere to each other. This property is crucial for predicting potential issues such as bridging or ratholing, where materials form stable arches or voids that obstruct flow. Cohesive strength is typically assessed using shear tests, which determine the stress required to cause relative motion between particles. High cohesive strength indicates a greater likelihood of flow obstructions. These shear tests can provide data to calculate hopper opening angles to avoid issues with flow.
2. Internal Friction
Internal friction refers to the resistance to motion between particles within the bulk material. It significantly affects flowability, with higher internal friction leading to poorer flow characteristics. Shear cell tests can measure internal friction. Being conscious of this property helps in designing equipment and processes that minimize resistance and enhance material movement.
3. Wall Friction
Wall friction is the frictional force between the bulk material and the surfaces of the equipment it contacts. This property influences how easily materials slide along hoppers, chutes, and other handling equipment. Wall friction is measured using wall friction tests, where a sample is sheared against a representative wall surface. Lower wall friction values facilitate smoother flow, reducing the risk of material hang-ups and improving process efficiency.
4. Compressibility
Compressibility measures the bulk density of a material under various applied pressures. It is an essential factor in storage and handling, as materials that compress significantly under load can experience changes in flowability and stability.
5. Moisture Content
Moisture content profoundly impacts bulk solids’ and powders’ flow behaviors. Excess moisture can lead to increased cohesiveness and caking, while insufficient moisture may cause dusting and segregation. Moisture content is measured using techniques such as oven drying or with moisture analyzers. Controlling moisture levels is crucial for maintaining optimal flowability and preventing material handling issues.
6. Particle Size Distribution
The range of particle sizes within a material affects its flowability and segregation potential. Materials with a broad particle size distribution tend to segregate, leading to inconsistent flow and quality issues. Particle size distribution is typically measured using sieving or laser diffraction methods. Finding out about this property aids in designing processes that minimize segregation and ensure uniform flow.
7. Particle Shape
The shape of individual particles influences how they interact and flow. Irregularly shaped particles may interlock, increasing internal friction and reducing flowability. Particle shape can be characterized using microscopy or image analysis techniques. Optimizing particle shape through milling or granulation processes can enhance flow properties.
8. Chemical Composition and Impurities
The chemical composition and presence of impurities can significantly impact flow behavior. Certain chemical interactions may enhance cohesion or lead to caking. Analyzing chemical composition through techniques such as spectroscopy or chromatography provides insights into potential flow issues and informs the selection of suitable flow aids or additives.
9. Particle Hardness and Surface Roughness
Particle hardness and surface roughness influence how particles interact with each other and with equipment surfaces. Hard, rough particles may increase wear on equipment and affect flow dynamics. Hardness can be measured using hardness testers, while surface roughness is assessed using profilometry. Recognizing these properties helps in selecting appropriate materials and designing equipment to minimize wear and flow resistance.
Inspect Your Materials and Their Characteristics With A Flowability Test
Accurately assessing key material properties in flowability tests is essential for predicting and optimizing the behavior of powders and bulk solids in industrial processes. By replicating actual process conditions during testing and employing specialized tests where necessary, industries can ensure efficient material handling, reduce downtime, and improve overall process performance. We, Jenike & Johanson, can offer our bulk material testing services to help you figure out your materials’ flow-related attributes. There have already been so many customers we have assisted, such as Titan Cement, and we want to do the same for you. Contact us today or look through our frequently asked questions page to find out more about our business.