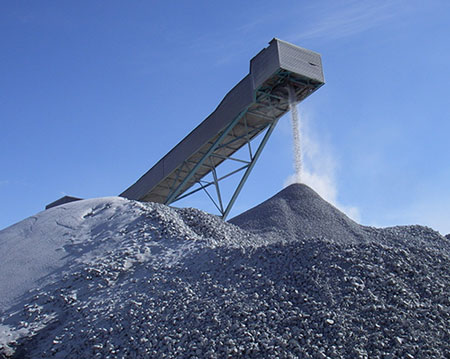
It was surprising for me when I recently received news that in yet another world-class mining project, or mega-project, the percentage of time of plant utilization (run-time) achieved is much lower than the plant availability. To appreciate the importance of this problem we must consider that the economic result (bottom line) of a mining operation with a modern milling plant is directly affected by the percentage of time that the plant is actually operating during a year (run time). Any time that the plant stops its operation means that less final product will be available to be sold, and consequently less income will be generated to pay for the huge investments involved in these types of projects.
In most mining projects a 365 days/year and 24 hours/day operation is considered, with plant run times of about 95% for semi-autogenous milling (SAG) plants and about 85% for modern crushing plants. The actual percentage of time that the plant operates after the start-up period should then be very close to these values — or higher. However, in practice the plant run-time is determined not only by plant availability (which is a consequence of the time required to maintain the equipment), but also by the availability of coarse ore to be fed to the SAG milling plant or to the fine crushing plant.
With a properly designed stockpile, the live storage capacity is high enough to provide coarse ore at the design flow rate whenever the plant requires it, so the percentage of time that the plant operates is very close to the plant availability. This is the ideal case; however, we have observed that in some large mining projects (recent and not so recent), the coarse ore stockpile has been designed without proper consideration of the ore’s flow properties. In most of these cases the result has been rathole formation, live capacities much lower than the desired value, and, as a consequence, the need for bulldozers or other mechanical equipment to push the ore from the dead volume areas into the ratholes. It must be said that the use of bulldozers, besides being a very expensive measure, may pose a high and undue risk for operators.
The major impact of the lower-than-desired live storage capacities on the economic result of the mine plus processing plant complex is orders of magnitude higher than the costs of an ore characterization and flow property testing program, followed by an adequate stockpile design. Apparently, a few project design engineers and project managers are still not aware of the available technology for the proper design of bulk solids storage and handling systems — or they are not giving proper consideration to the economic aspects related to the achievement of the design stockpile live storage capacity during plant operation.
Let us help ensure your success with your gravity reclaim stockpile design, contact us today!