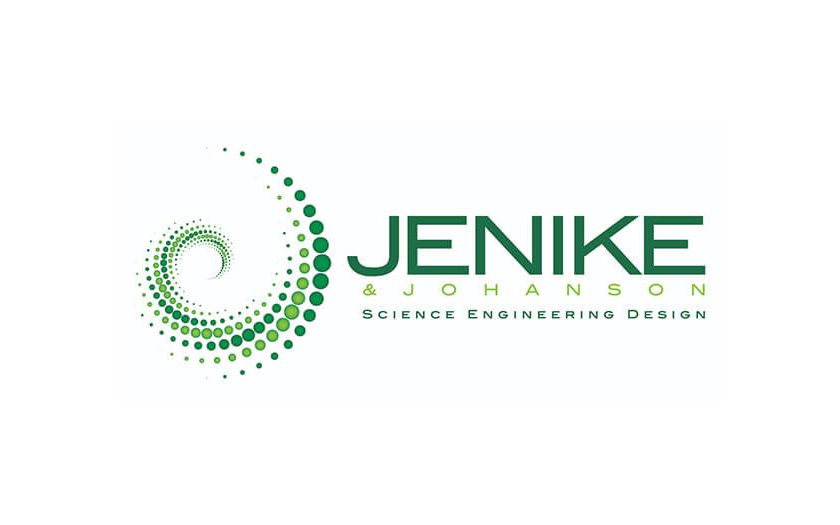
Loss-in-weight feeders are a common feature of many solids handling processes. Many vendors offer well developed, sophisticated systems that are generally easy to operate, maintenance friendly and available in a wide range of sizes to fit feed rates from a few kg/hr to 1,000’s of kg/hr. One of the recurring problems we see as consultants is the misunderstanding of how these systems work and how their feed specifications should be characterized when continuous loss-in-weight feeding is required. It is not uncommon to see a customer describe a feed requirement in terms of the required feed rate plus or minus a certain percent. Something like “the feeder should deliver 1,200 kg/hr, +/- 1% .” This seems reasonable, but interpreting exactly what this means is not always clear. Some people would interpret this to mean that the feeder should deliver at least 1,188 lb and no more than 1,212 lb in any given hour. Others could interpret this to mean that the feeder should deliver at least 19.8 kg and not more than 20.2 kg over a 1 minute time period, which would end up at the same weight after an hour, but would potentially have less variation throughout the one hour time period. Clearly the sampling method is important in describing the feeder performance, and the frequency of sampling ultimately depends on the process requirements. Evaluating the performance of a feeder requires taking a sufficient number of samples to characterize the system and defining the time interval between samples so that the evaluation is meaningful for the process. These could be physical samples taken in a bucket or virtual samples taken by the feed system controller. Processes that have a short residence time and require tight control of product composition will require sampling at short time intervals to accurately measure (and ultimately control) what is going into the process. Extruders typically have residence time measured in seconds, requiring samples taken at a fraction of this time to be meaningful. Other processes operate on longer time scales and don’t require sampling at this frequency.
Because rate is a calculated value that must be determined from weight measurements taken over time, the shorter the time interval the less accurate the measurement for a given system. Taking the simplest approach, and assuming that what is important for the example given above is that the average rate is 1,200 kg/hr when evaluated for 30 samples taken at 30 minute intervals, then the time base for the measurement would be 30 minutes, and the allowable range of measured weights delivered during each period would be 594 kg to 606 kg. If the scale measuring the weight has a capacity of 2,000 kg and has an error of +/- 0.01% of full scale, then the error in measurement would be plus or minus 0.2 kg, which is just barely acceptable for our desired error band of 12 kg. However, if we need to know the rate on a shorter time scale the accuracy of the scale becomes important. For example, if we wanted to take 30 samples at 1 minute intervals, then this scale will be inadequate because the difference in weight between each sample would be 19.8 kg to 20.2 kg, which is too small a difference for the scale to measure accurately. Measuring rate over a short time period generally requires a smaller overall total weight of the measurement system and more precise scale equipment in addition to sensing equipment that can filter out noise to provide a clean weight signal.
Carefully considering the rate requirements for a system in terms of the required accuracy and time interval over which measurement is important will ensure a successful installation at the lowest cost.
Another problem area related to loss-in-weight feeders is trying to use a loss-in-weight feeder to correct feed rate problems with a poor handling material. Even when a loss-in-weight system is well adapted to the feed requirements in terms of time scale and weighing requirements, problems with reliable operation of the feeder can result in poor performance. Many fine powders and other cohesive materials flow poorly from bins and hoppers that are not designed to handle cohesive or floodable materials. This leads to poor rate control in many cases and the misapprehension that using a loss-in-weight control scheme can fix the problem by incorporating a control system to deal with the erratic feed problems. In most cases adding a control system to correct problems like this fails. Loss-in-weight control systems should be viewed as enhancements that can make an already well operating volumetric feed system better and not as add-ons that can fix a poorly operating system.