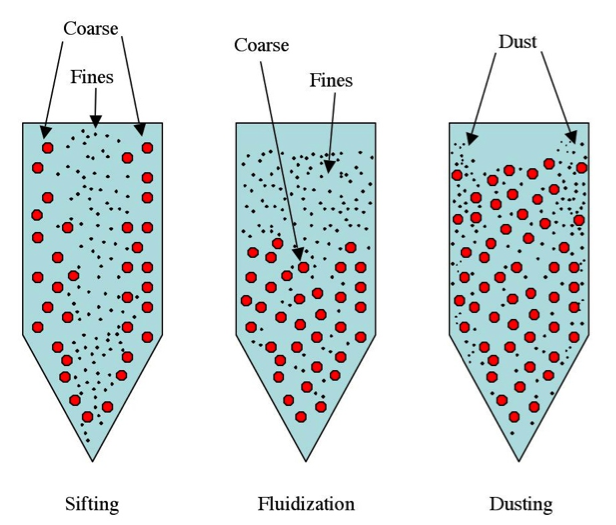
If you are handling a blend of powder ingredients such that some of the ingredients are relatively fine and others are coarse, did you ever experience that the ingredients were separating during handling? Were you ever left wondering where did the finer ingredients in the blend disappear? Have they gone with the wind or slipped through the cracks?
In many industries, production process involves mixing or blending of various ingredients. Usually, each of these ingredients has a specific role such that all of the ingredients need to stay together in the product in a specific proportion. Common examples are blending of actives and excipients during pharmaceutical tablet compression process, mixing of metal powders to form a P/M part, mixing of various cleaning agents during detergent manufacturing, and so on.
Sometimes, you may hear the notion that it is all about blending. Take care of the blending, and you will have a perfect mix. However, that is only one side of the coin. A perfect blend does not guarantee a perfect product. Every time a transfer step occurs in the powder handling process, the mix / blend is presented an opportunity to separate. Thus, towards the end of the process, the constituents of the blend might not remain as uniform as at the end of the blending.
Even if you are not handling a mix of different ingredients but your material itself has a wide particle size distribution, the fines and the coarse particles in the material can separate from each other during handling. This can lead to feeding concentration of fines or coarse particles at times, which can affect processes where surface area and bulk density are important.
Such separation of a blend or a material into regions of fine and coarse particles is termed as particle-size-segregation or simply, segregation. There are several driving forces or mechanisms that can cause segregation. The most commonly occurring mechanisms in the industry are sifting, fluidization and dusting. When sifting segregation occurs, fines sift through the gaps between coarse particles, and accumulate directly beneath the fill point. This typically results in a horizontal separation of fines and coarse ingredients/particles in a bin/vessel such that the fines concentrate around the central region and the coarse particles concentrate near the periphery. Fluidization segregation usually results in a vertical separation to cause fines to accumulate near the top and coarse particles to accumulate near the bottom. Dusting segregation usually causes the superfines in the material to drift with the air-currents in the vessel and settle along the walls or near the periphery.
If you are in the early stages of developing formulation for a product, segregation problems may be addressed by changing the particle size distribution of the ingredients to minimize separation tendencies. However, many times, segregation problems are realized during commercial production stage. In such cases, while you may not be able to change the formulation, you can consider making changes to the production process to minimize handling and transfer steps. If even that is not possible for one reason or another, you have to resort to changing / modifying powder handling equipment such as hoppers, feeders, conveyors to minimize segregation during handling.
The key to addressing any segregation problem is to first understand which mechanism(s) are causing the segregation to occur. Once this is understood, the next step is to identify processes or operations where these mechanisms are introduced. Then, such steps should be eliminated or modified to minimize segregation and achieve uniform product. Segregation tests as well as flow properties tests provide significant information to aid in solving segregation problems.