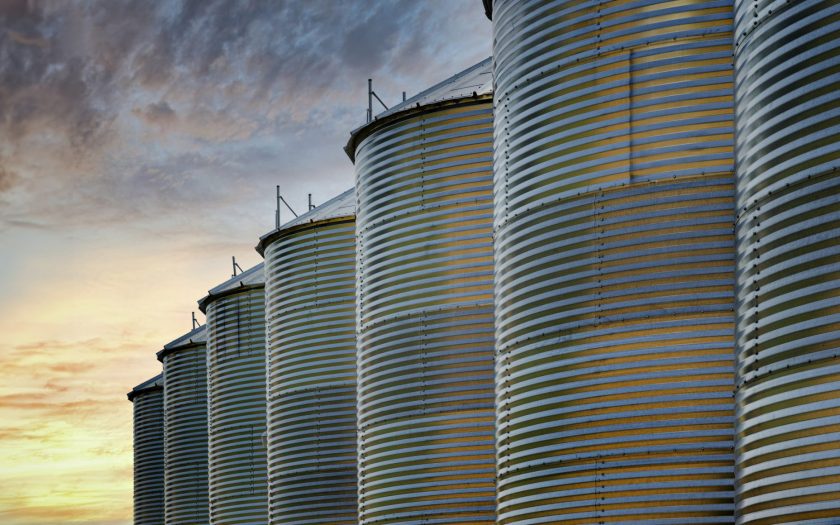
Building silos demands more than just strong walls; it requires precision in managing how materials move within. Silo engineers tackle a dynamic challenge where forces constantly shift, influencing both stability and efficiency. Every detail, from how materials flow to how structures stand, hinges on understanding these ever-changing dynamics.
Understanding Silo Dynamics
Dynamics in silo engineering refer to the forces and motions that occur within and around the silo structure. These can be caused by various factors, including the flow of materials during filling and discharge, vibrations from nearby equipment, or even external forces like wind or seismic activity. Unlike static loads, which are constant and predictable, dynamic loads are variable and can lead to unpredictable outcomes if not properly accounted for in the design phase.
One of the primary dynamic challenges in silo engineering is silo quaking. This phenomenon occurs when bulk materials, especially fine powders, compact during storage and then suddenly release when the material below is discharged. The rapid flow of material can create vibrations and shock waves that travel through the silo structure, potentially leading to structural fatigue or failure if not mitigated. Silo thumping, a related issue, happens when air pockets trapped within the material suddenly collapse, causing a loud thumping sound and a momentary increase in pressure on the silo walls.
The Role of Flow Patterns
The flow pattern of materials within a silo significantly influences dynamic behaviors. Engineers typically design silos for one of two flow patterns: mass flow or funnel flow. In mass flow, the entire contents of the silo move as a single body, with material at the top moving down as material is discharged from the bottom. This uniform movement helps minimize dynamic forces but requires careful design to ensure consistent flow and avoid blockages.
Funnel flow, on the other hand, occurs when only a portion of the material flows while the rest remains stationary. This pattern is more prone to dynamic issues, such as arching and ratholing, where the material forms stable structures that can collapse unexpectedly, leading to dynamic loads on the silo walls. Engineers must carefully consider these potential issues when selecting and designing the appropriate flow pattern for a given material.
Material Characterization and Dynamic Effects
Understanding the physical properties of the materials stored in silos is essential for predicting and mitigating dynamic effects. Factors such as particle size, moisture content, and bulk density all influence how a material behaves under different conditions. For example, materials with high moisture content may clump together, leading to uneven flow and increased dynamic loads during discharge.
Dynamic effects are also influenced by the interaction between the material and the silo walls. The friction between the two can cause the material to stick, leading to uneven flow and increased pressure on certain areas of the structure. This is particularly problematic in funnel flow silos, where the stationary material can create high localized loads when it finally breaks loose.
Mitigating Dynamic Challenges in Silo Design
Engineers employ several strategies to mitigate the dynamic challenges associated with silo design. One of the most effective is the use of vibration analysis during the design phase. By simulating the dynamic loads that the silo will experience during its operation, engineers can identify potential weak points and reinforce them before construction begins.
Another approach is the use of shock absorbers and dampeners within the silo structure. These devices help absorb the energy from dynamic loads, reducing the impact on the silo walls and extending the lifespan of the structure. In some cases, engineers may also design the silo with a slightly flexible structure, allowing it to absorb and dissipate dynamic forces more effectively.
The Importance of Integrated Engineering
Dynamic considerations in silo engineering are not isolated; they interact with other aspects of the design, such as structural integrity and material handling efficiency. For this reason, a multidisciplinary approach is essential. Engineers must work closely with material scientists, structural engineers, and equipment manufacturers to develop silo designs that account for all potential dynamic effects.
By integrating these considerations into the design process, engineers can create silos that are not only structurally sound but also capable of handling the dynamic challenges posed by the materials they store. This holistic approach ensures that the silos will perform reliably over their operational lifetime, reducing the risk of failures and enhancing overall efficiency.
Closing Thoughts
At Jenike, we understand that effective silo design requires more than just structural integrity; it demands a deep understanding of the dynamic forces at play. By addressing these factors early in the design process, we ensure that your silo systems are robust, reliable, and tailored to the unique properties of your bulk materials. Our expertise in conceptual and functional engineering allows us to integrate dynamic considerations seamlessly into every project, reducing the risk of operational disruptions and enhancing the efficiency of your storage solutions.
If you’re looking to optimize your silo systems, explore our Conceptual and Functional Engineering services to see how we can help you design silos that stand the test of time.