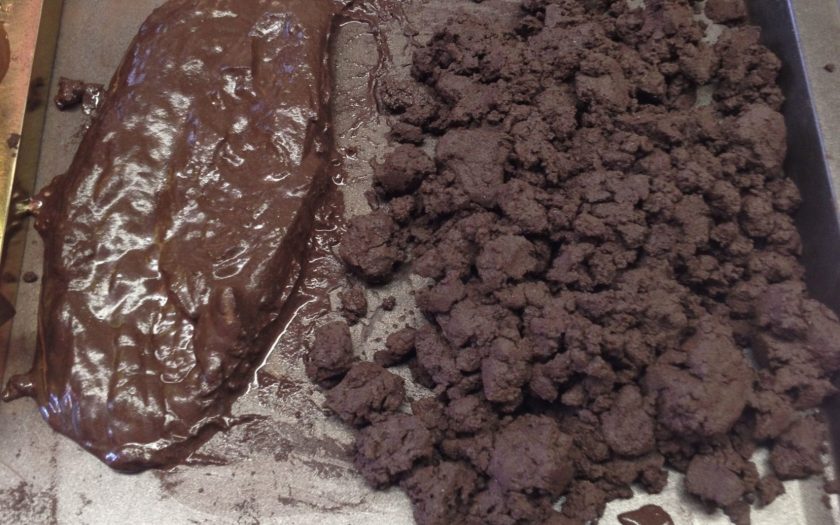
A few weeks ago I was onsite at a port loading facility. As I walked around watching the ships being loaded, I started thinking of all of the ships being loaded with bulk solids cargoes, not just here in Australia, but all around the world. In 2009, two ships capsized and sank following liquefaction of iron ore cargoes after having been loaded in Indian ports during the monsoon season. In 2010, there was a further loss of three bulk carriers carrying nickel ore loaded in Indonesia.
Achieving cost effective transport of materials is important to producers and exporters but the need to accurately determine the Transportable Moisture Limit (TML), the maximum moisture content of a bulk material considered safe for transport in bulk cargo vessels, is also of great importance. Preventing the liquefaction of all cargoes at sea is clearly the end game, but how to get there, is the immediate question.
Currently, in Australia, much research is being conducted with regard to modifying/improving the Proctor/Fagerberg test method (outlined in Appendix 2 of the IMSBC Code 2012 edition) used to determine TML in at least six key areas; particle density, sample consolidation, segregation, starting moisture content, the selection of a reasonable TML value, and particle size distribution.
In my mind, all of these areas have a role to play in developing both an accurate and yet “real world representative” determination of TML values. The moisture content of a bulk solid will vary depending on the sample’s particle size distribution. Measured TML values may either increase or decrease as materials become coarser, however, if the TML value is measured using larger/coarser size distributions (>5 mm top size), a situation could result in which the overall moisture content of the whole material is below the TML value determined for that material, yet the moisture content of the finer distribution (<5 mm) could be above the TML value for the whole material and/or above even the finer distribution’s TML value.
There are cases of iron ores being shipped safely in other locations around the globe at higher than measured TML values. If the standard is changed to include, for example, TML determination at 80% or 85% of saturation, then the fines present in the sample might be even closer to their saturation value, particularly if larger particles, >5 mm, are included in the determination of the TML value. I just hope that we don’t lose sight of how important all of the key areas are in the determination of TML.