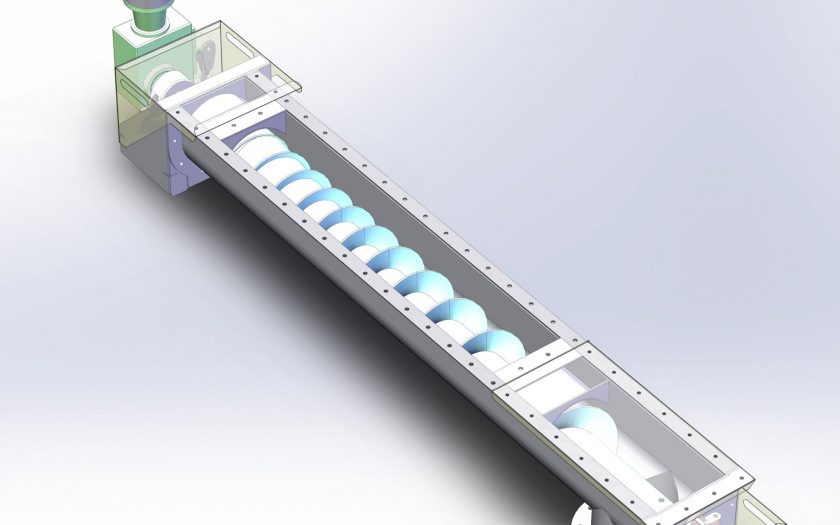
You’ve learned your lesson in the past, and struggled with solids handling problems that caused untold problems during start up, completely unrelated to your key technology. And even now, the process runs below its design capacity and requires unanticipated babysitting. So this time you’ve gone to the effort to measure your material’s flow properties and worked with a Jenike & Johanson engineer to develop an appropriate bin design to avoid an encore performance. But in addition to the bin design, J&J recommended a feeder with very specific features that look like they will be unnecessarily expensive. And the drive power seems unusually high for the size of the equipment. Sure, it will work, but is it overkill? Is this really necessary to function reliably?
Feeders are, in fact, mission critical when it comes to reliable solids handling. An improperly designed feeder can, and frequently does, convert a mass flow bin to a funnel flow discharge pattern. This can happen in any mass flow design, but nowhere is this more obvious than when a feeder is used under a hopper with a long, narrow, slotted outlet. This type of hopper is typically used when handling difficult materials, either because they are prone to arching and ratholing, are highly frictional, or because they are susceptible to discharge rate limitations.
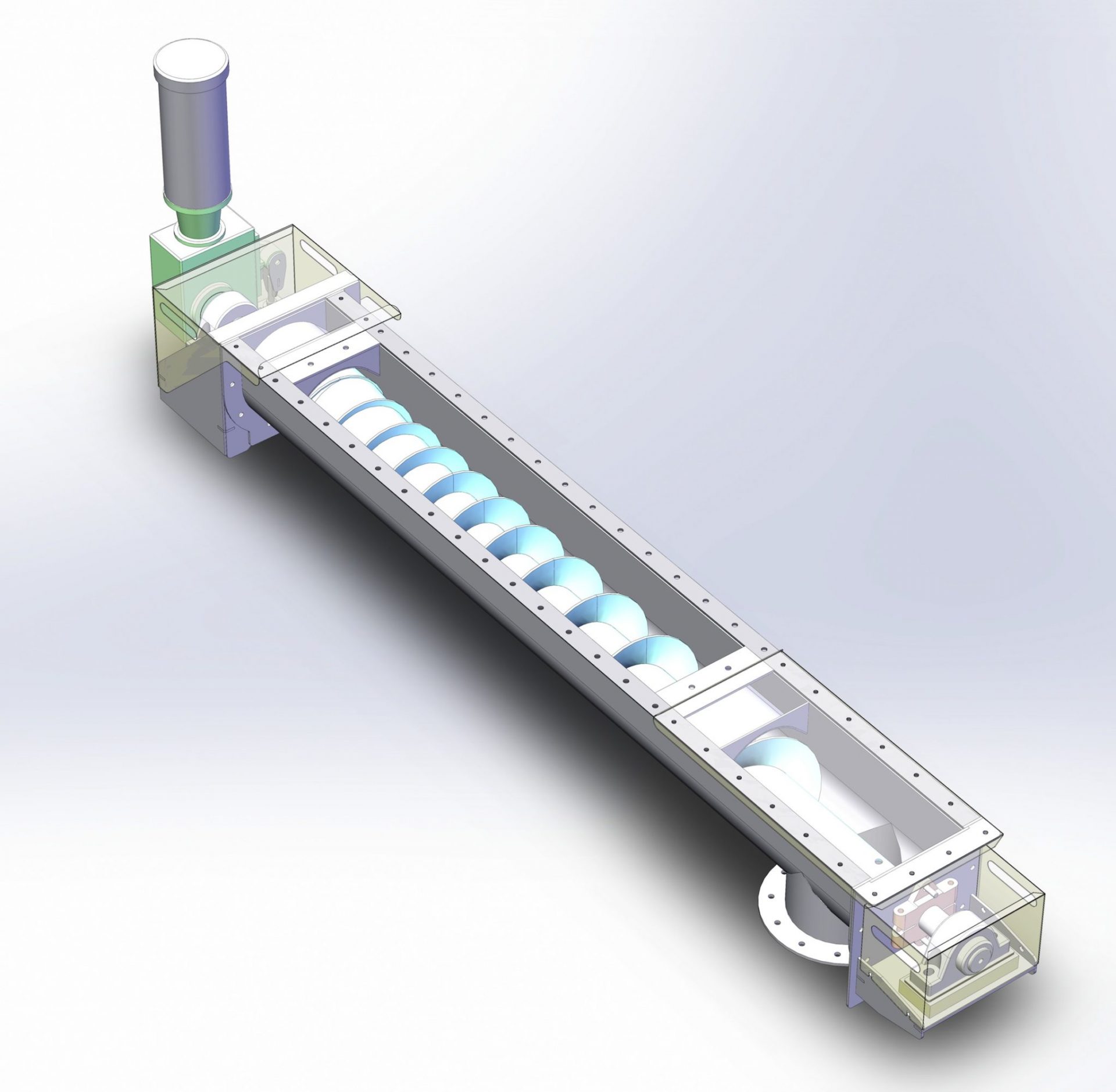
For such a bin to operate as intended, the feeder has to remove material from every square inch of the hopper outlet. This requires that the feeder is carefully designed to provide a consistent increase in capacity along the entire length of the hopper outlet. Anything less can render all of the careful engineering that went into your bin design null and void. And yes, operating power can be relatively high when compared to a conveyor of equal size. This is because of the solids pressures acting directly downward, onto the feeder, and because of the size of the shear plane that has to form between the downward flowing material leaving the hopper and the horizontally flowing material in or on the feeder. Conveyors are not subject to such vertical and shear loads and therefore typically operate at much lower power.
When it comes to feeder design, don’t take shortcuts. What might appear to be a means to reduce cost is likely to result in untold trouble during startup, and for many years to come.