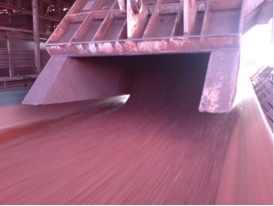
New, innovative solutions are being developed to transport more materials faster, along routes and across terrains that would not be possible not long ago. Higher belt speeds and variability in materials make it even more important to get the fundamentals correct, like getting the load centered on the belt quickly and efficiently at each loading and transfer point. Not only does this make the conveying easier but it also reduces spillage, belt wear, dusting and material attrition.
Methods of transferring bulk solids still widely used, are to slam the material into a rock box to kill its momentum and then let it fall onto the receiving belt. The receiving belt is used to accelerate the material up to the belt speed. This does not work for high belt speeds and high tonnage rates and is not a good method even at lower rates.
Dropping the material vertically onto a belt requires an “acceleration zone” where large rocks bounce and roll, creating a belt wear problem, air is entrained in the fines to create a dust problem, and the particles exchanging energy can create a material attrition problem as well. These problems are compounded if the receiving belt is inclined.
Variability in the material, such as particle size or moisture content, will make the buildup in the rock box change and alter the flow through the rock box. If the material drops through the rock box off-center, the receiving belt will be loaded on one side. This will often result in spillage at the loading point, or if the belt is forced to ride up on the idlers eccentrically, spillage along the route. Trying to keep a large, high-speed belt centered with training idlers under these conditions is very difficult and will often result in more belt wear.
A correctly designed and efficient transfer point will eliminate these problems because the transfer chute handles the load relatively gently in spite of the high speeds and correspondingly high accelerations. By placing the material on the belt centerline at a speed close to the belt speed, the belt can easily convey it efficiently without spillage.
Instead of killing all the momentum of the material entering the chute, momentum can be used to keep the speed of the flowing material close to the belt speed all the way through the chute. Slowing the flowing stream of material down, requires that the cross sectional area increase. This is the beginning of a blocked chute. Also, slowing the material down and then accelerating it again so that the cross section changes rapidly, is an ideal way to entrain air and create dust.
Balancing the friction in the chute that slows the material down with gravity accelerating the material as it drops from the level of the incoming to the level of the receiving belt can be used to keep the speed through the chute more-or-less constant. Keeping the material in contact with the chute surfaces as much as possible reduces the possibility of entraining air. This also reduces points of impact and the wearing away of the chute at those points.
Placing the material on the receiving belt centerline at a speed close to the belt speed is also the best way to reduce belt wear and dusting at the interface between the material and the belt. If the chute is designed properly there should not be a need for an enclosed “acceleration zone” with a dust extraction port.