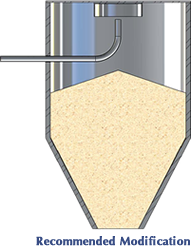
The Need
A major cake mix manufacturer was experiencing unacceptable variations in several of their final mixes. Jenike & Johanson was called in to solve this segregation (demixing) problem. From our observations and additional plant processing data, we determined the chief source of ingredient demixing was an often-overlooked one: the pneumatic conveying system.
Pneumatic conveying is widely used to convey bulk solids due to its many advantages. It is a versatile, safe, relatively simple, inherently clean, and automation-friendly method of material transfer. On the other hand, pneumatic conveying introduces new handling concerns, especially with mixtures. A common – and costly – problem associated with pneumatic transport is particle segregation or demixing. Demixing can occur by air entrainment (fluidization), sifting, or particle entrainment in an airstream.
One of these segregation mechanisms was occurring at the end of the existing transfer line, where entrained particles are disengaged from the airstream. The mixture’s smallest particles, which are the easiest to move, tended to settle farther from the inlet than those of greater size and mass.
The orientation of the conveying line as it entered the hold bin also contributed to the problem. The convening line entered the top of the bin, and directed the incoming stream of material down into the center of the bin. The kinetic energy of the incoming air/material stream contributed to the tendency of the bed of material in the bin to remain fluidized, allowing fluidization segregation to occur. This resulted in a layer of fines at the surface of the material in the bin.
The Solution
Armed with observations from our site visit and the results of lab testing that measured the handling characteristics of the cake mix, we were able to confidently design a solution without wasting time and money on a trial-and-error approach.
The first part of our recommendation was to revise the sequence of ingredient addition. By adding one of the major ingredients earlier in the process, the blend was made more cohesive (less free flowing). As with many blends, this reduced its tendency to segregate.
We then recommended increasing the diameter of the conveying line at several locations. These successive diameter increases controlled the discharge air velocity and segregation caused by particle entrainment.
To minimize fluidization segregation, we recommended rerouting the conveying line so that it discharged the material vertically up and into a target box. This diffused the energy of the discharge stream and allowed the particles to settle out more gently across the pile’s top surface.
Finally, we recommended that the hold bin be modified to ensure a mass flow so that the effects of any remaining side to side segregation would be minimized during discharge of the bin.
The Result
Pneumatic conveying is a highly useful technology, but one with problems all its own. Solving – or, more importantly, preventing – these problems requires a thorough understanding of the flow characteristics of the bulk solids being conveyed as well as the effects of air-driven transfer on ingredient mixtures.