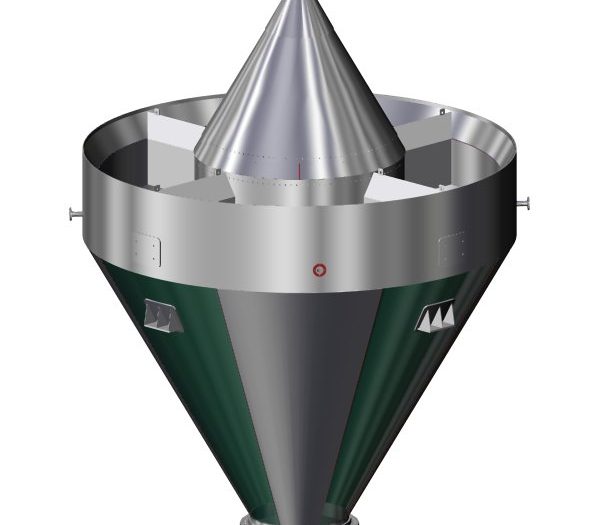
The Need
A new polypropylene (PP) plant was built by BP Amoco Chemical at Geel, Belgium in 1995. The 200,000 ton/year PP unit used the BP Amoco gas phase process and BP Amoco’s high-activity supported catalyst. The plant produced random and blocked copolymers and a wide range of homopolymers. When it came on line in late 1996, it doubled BP Amoco’s European PP capacity.
A purge column was included in the design downstream of the reactors. The purge column provides several important functions in a gas phase process. First, it reduces residual volatiles to an acceptable level using nitrogen as the purge gas. Second, it deactivates the trace catalyst residues by using a small quantity of steam. Third, it provides surge capacity between the reaction and pelletization operations.
In spite of the benefits of gravity flow processing vessels, problems can occur that limit their effectiveness. Incomplete purging or nonuniform conditioning can be caused by localized fluidization, nonuniform gas distribution, and nonuniform solids velocity profiles and result in off-grade product, fire/explosion risks, environmental compliance issues, or downstream handling problems. Other problems include excess purge gas usage and product cross-contamination during grade changeovers.
The Solution
The first steps were to define the process requirements and to determine the properties of the solids and gas that were being used.
Since for most continuous flow processing vessels a solid’s residence time in the vessel is critical. Solid’s residence time in the vessel can be controlled if the flow pattern through the vessel is mass flow, which results in a first-in-first-out flow sequence. In order to design a mass flow processing vessel with gas injection, the flow properties of a material must be known. We measured the critical flow properties, which included cohesive strength, wall friction, range of bulk densities, and permeability.
For this application, engineers at BP Amoco specified the minimum and maximum purge duration (i.e., time of exposure to purge gas). They also specified the required solids and gas flow rates as well as the gas temperature and pressure at the top of the vessel.
Based on the flow properties measured for BP Amoco, engineers at Jenike & Johanson developed the functional design of this purge column. It consisted of a tall, narrow cylinder section, below which was a steep-sided conical hopper. Purge gas was introduced just above the top of the conical hopper section using our patented J-Purge™ technology. The design provided a uniform distribution of the purge gas, with no adverse effects on the flowing solids.
The Result
The purge column has been in operation now for over a decade and has performed very well, meeting the design basis. This technology has been incorporated into three other plants which use BP Amoco’s gas phase process: BP Amoco’s Chocolate Bayou No. 4 PP, shown in the photo, and two licensees.