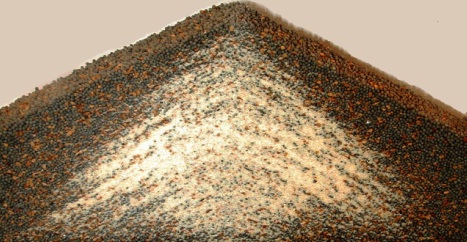
The Need
A domestic pharmaceutical manufacturer was producing a highly segregating direct-compression blend of an active pharmaceutical ingredient (API) and excipients like sucrose, lactose, and microcrystalline cellulose. After blending, the material discharged from a twin-shell mixer and experienced heavy [popover image=”/your-needs/segregation-sifting-pile-5/” link_text=”sifting segregation” title=” ” content=”Sifting segregation mechanism” direction=”right”] during flow into a portable container.
The segregation effect yielded a high concentration of fine particles in the container’s center, while the material at the periphery was mostly coarse. Given that the container discharged in a funnel flow pattern, the fine particles (high in active drug content) discharged first, followed by the coarse material, which was sub-potent.
Jenike & Johanson was hired to assist in determining the cause of the problem and to recommend a cost-effective solution.
The Solution
Knowing sifting segregation was occurring during container filling, Jenike & Johanson recognized that mass flow discharge would effectively reblend the segregated mixture during discharge. However, based on the flow properties of the blend, the existing portable containers were not capable of cost-effective modifications required to achieve mass flow. Consequently, a new mass flow container design was required. Jenike & Johanson engineers developed a prototype BINSERT® container design that met the constraints of fitting into the existing system configuration while meeting the necessary batch volume.
The Result
Given the success of the prototype mass flow BINSERT® portable container in eliminating blend segregation while providing consistent reliable flow, our client ordered additional units to meet the needs of the flexible production manufacturing environment. An additional benefit resulting from this mass flow container design was the achievement of reduced tablet weight variability due to improved bulk density consistency of the blend being fed to the tableting press.