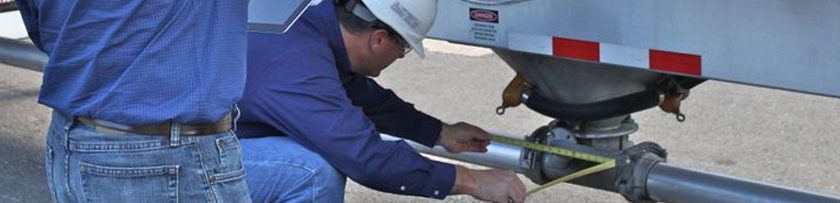
When people ask me what I like best about my job, lots of things come to mind but the answer is easy. I love the feeling of accomplishment that I get from being able to point at something and say “I did that!”, and if that something is a success, the feeling is even better!
The question of what I would change about my job, is a bit tougher. I like to do things right – from the start – every time, and I like to fix everything. This part of my nature often gets me in trouble with my friends and family, especially with my husband who is not an engineer! At J&J a very high proportion of projects that I get involved with are projects whose bulk material handling system is preventing the project from being a success, and the source of the problem- and hence the solution – seems to be consistent. More attention needs to be paid to bulk material handling, by people who really understand bulk material handling, at the early stages of a project. That’s what I’d change.
I admit that I am torn, because if all handling systems were designed correctly, some of the work I get to do would disappear, however my true nature sees a problem and wants it fixed. And, of course if my message does as I hope it will, I will get some different work, which I’d probably like better. To that end I’d like to point to three articles by Edward Merrow, “A Quantitative Assessment of R&D Requirements for Solids Processing Technology”, “Estimating Startup Times for Solids-Processing Plants”, and “Problems and Progress in Particle Processing”. In these articles Merrow provides evidence to support my message. For your project involving bulk material handling to be a success, experts must be involved at the early stages. They must perform appropriate testing (both bench scale and pilot scale) and then be involved in the basic and detail design stages. It’s either that or you need a lot of luck on your side.
Many of our new clients come to us because they are commissioning a project that is currently experiencing bulk material handling related problems that are stopping or limiting production. They require immediate and decisive solutions. These projects are often green field, but modifications to an existing facility to accommodate changes to feedstock, throughput, and/or equipment, often result in troublesome start-ups if design did not properly consider material handing at a sufficiently early stage. In addition, because of physical constraints, the solutions here often tend to be a compromise over what would have been recommended in an earlier phase.
Because of how engineering projects tend to evolve, and how funding is determined, even those clients who have seen, first-hand, the potential material handling pitfalls that can occur, are often unable to involve experts in the earliest phases of a project. The leading reason to involve material handling experts is to avoid handling problems and of course that is not necessary until the project has had the necessary financial studies, has been deemed to be profitable, and now needs detailed engineering. The problem with this approach is that by this time, either the project constraints are sufficiently set that handling system is compromised or making the required changes to accommodate the handling system’s requirements is difficult, time consuming, and expensive.
I believe that experts should be involved in the very first phases to provide design basis flow properties, to review material handling system concepts and preliminary designs from a flowability viewpoint. In fact, this can help to steer the project in the most profitable direction. For example, in a recent project I was asked to review the design of a concentrate storage bin for a mineral processing plant being commissioned. When we measured the flow properties of the concentrate, we found that as long as it was kept moving, hopper outlet sizes were reasonable. However, after storage time, they were impractically large. Making modifications to the bin would be a compromised solution that would still limit operations and would require significant capital. If these results had come to light earlier in the project, the handling system would have been designed differently.
On the surface, it might seem more expensive to involve the experts in the early stages, but I would argue that it is money well spent. I sometimes tell clients that they should think of the cost as insurance, but recently the words of one of my clients made me realize it’s actually better than insurance, it’s assurance. We had already worked for him on two projects that had experienced problems during start-up when he called and said that he’d like to “try something novel and involve us at the start of the project”. Later, with the project due to be commissioned, I called to ask him how everything was going. He replied that he had no worries and was sleeping well.
If you are starting a new project involving material handling, it is my genuine hope that this blog strikes a chord with you. It seems obvious that money spent building something that does not do what it was intended to do, is wasted.
So there you have it. Assurance vs insurance, it’s a no brainer!