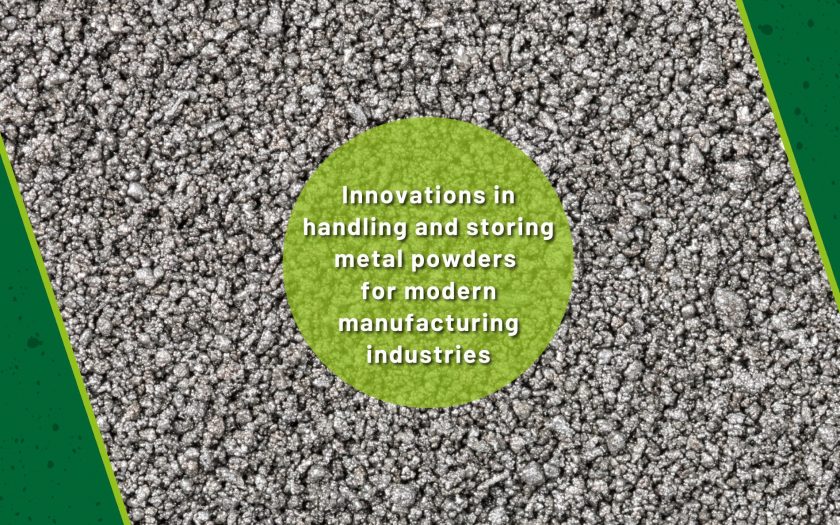
Metal powders are essential to modern additive manufacturing. They support the production of lightweight aerospace components, enable custom, intricate biomedical implants, and form a wide range of parts for automotive, lawn, appliance, and next-generation electric vehicles. To unlock all their advantages, the flow of these materials must be well-controlled in the production environment. Because of their unique physical and important metallurgical properties, metal powders demand a high degree of control throughout processing.
As production volumes grow, near net shapes become more exacting, weights are minimized, and expectations for performance become increasingly demanding, legacy methods of handling and storing metal powders often fall short. The industry faces an important question: how can manufacturers manage metal powders safely, efficiently, and consistently without compromising quality or putting operators at risk?
Addressing this question has become more than a process upgrade. It is a strategic imperative. Fortunately, new innovations are emerging that reimagine how metal powders move, how they are protected, and how they are controlled throughout the manufacturing lifecycle.
The Hidden Costs of Poor Powder Management
Mishandling metal powders introduces risks that extend far beyond the material itself. Flow interruptions can stall production lines. Contamination can degrade product performance. Uncontrolled dust or exposure can lead to serious health hazards, regulatory infractions, or even catastrophic energetic events within the process or facility. What begins as a minor material issue can escalate into major financial losses as well as quality, compliance, and operational continuity problems.
Innovations in Metal Powder Handling
Transferring metal powders demands far more than just moving material from one vessel to another. These processes require effective control mechanisms that maintain flow integrity, safeguard personnel, and protect material properties at every stage.
Enclosed Transfer Systems with Minimal Exposure
Manual, open-air handling is quickly being replaced by sealed gas and vacuum-based systems. These technologies preserve powder quality by limiting exposure to air and contaminants. They also enhance worker safety and reduce material loss.
Conditioning Equipment for Consistent Flow
Metal powders can become less free-flowing over time due to environmental exposure. Conditioning with controlled environments can ensure reliable flow characteristics. Integrated sieving ensures uniform particle size for stable, high-quality output in AM and compaction operations.
Static Control and Explosion Mitigation
To minimize combustion risk in reactive metal powders, modern systems integrate electrostatic discharge protection, non-spark-inducing materials, and explosion-venting mechanisms. Many facilities are now built with inert gas suppression as an added layer of safety in high-risk environments.
Precision Feed Systems for Downstream Equipment
Accurate delivery to pressing and sintering stages is crucial for maintaining uniformity. Feed systems designed for the tight control of flow rate and composition help eliminate part defects and streamline repeatability across production runs.
Innovations in Metal Powder Storage
Storage conditions directly affect powder stability, safety, and usability. The latest storage technologies extend far beyond basic containment, providing tailored environmental controls and intelligent management systems.
Inert Gas Cabinets and Sealed Containers
For metal powders that oxidize rapidly, sealed environments filled with argon or nitrogen preserve metallurgical integrity. These conditions help keep powders stable without risking reactivity during storage.
Humidity and Climate Control
Preventing moisture exposure is critical in some operations. Climate-controlled storage systems now feature built-in desiccant regeneration and real-time sensors to maintain consistent low-humidity environments, which protect powder flowability and prevent degradation.
Intelligent Inventory Management
Barcoded and RFID-tagged bins offer detailed tracking from initial storage to final use. Manufacturers gain full visibility into powder age, reuse history, and condition, helping to track materials and supporting full audit compliance.
Bulk Storage Solutions for High-Volume Applications
In high-throughput manufacturing, metal powders need to be both readily available and easily controlled. Scalable modular hoppers and automated dispensing stations now support efficient bulk management, reducing manual handling while maintaining material separation.
Engineering Powder Systems with Purpose
Understanding how a powder behaves under varying conditions is crucial for designing systems that truly perform. At Jenike & Johanson, our work begins with detailed material testing and analysis, followed by tailored engineering solutions that align with real-world operating conditions.
Rather than focusing solely on individual components, we consider the complete process—from initial containment to final compaction. Whether the goal is preventing flow stoppages, maintaining flow consistency, or improving safety, our approach connects material science to practical system design with measurable results.
Elevating Powder Management Across Industries
Metal powders are central to manufacturing sectors that demand high-performance materials, including aerospace, automotive, and medical device production. Powder handling and storage systems must operate with precision, maintain uniformity under compaction, and offer the scalability needed for continuous production.
The most effective solutions integrate environmental control, data-driven oversight, and purpose-built engineering. At Jenike & Johanson, we deliver precisely that. Our approach combines material science, engineering expertise, and hands-on experience to help manufacturers handle and store metal powders with confidence. Powdered metals testing conducted by our team provides the data needed to design systems that perform reliably under real-world conditions. Consistency, safety, and reliability aren’t optional, they’re vital. That’s why we design systems that deliver on all three, every time.