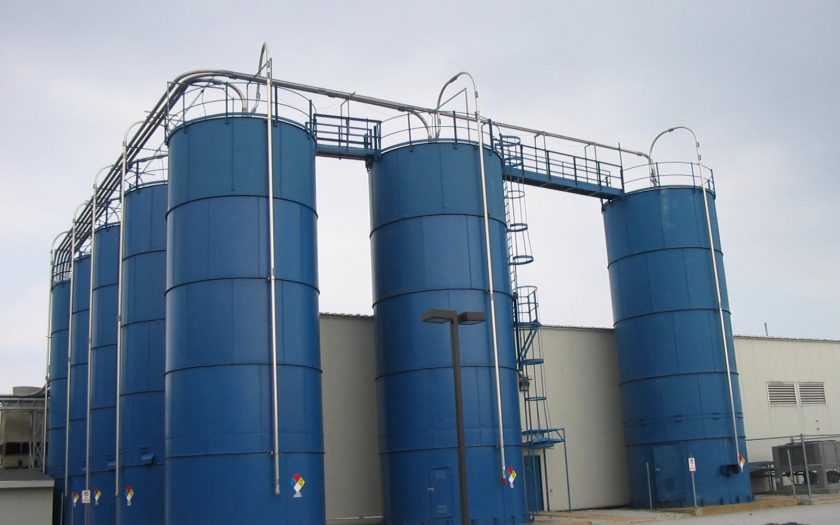
Efficiency, reliability, and precision are at the core of effective bulk material handling systems. Designed to manage large volumes of materials seamlessly, these systems rely on specialized equipment to optimize flow, storage, and processing. Every component plays a critical role in maximizing performance and minimizing operational downtime.
In this guide, we’ll explore the key categories of equipment that drive the efficiency and effectiveness of bulk material handling systems.
Silos and Bins
The terms silo and bin are used interchangeably to describe a vessel for storing bulk materials like grains, minerals, and powders. It is essential that these vessels be engineered to suit varying material properties, including flow characteristics and moisture content. Key components of a silo or bin are:
- Cylinder. Typically circular, square or rectangular in cross section, this provides most of the storage volume.
- Hopper. Positioned below the cylinder, this funnel-shaped container directs the stored bulk solid into a feeder or conveyor. When designed properly, it promotes controlled, gravity-driven flow of material, ensuring consistent flow rates and reducing the risk of blockages.
- Slide or pin gate. This isolates the hopper from the feeder so the feeder can be maintained while the silo or bin still contains material. In some cases it can be used to regulate the flow of bulk materials without the use of a feeder.
- Expansion joint. Sometimes used to accommodate thermal expansion and mechanical movement, protecting system integrity.
- Feeder. This regulates the discharge rate of bulk material from the hopper. Common types include:
- Screw Feeder: Utilizes a rotating helical screw to move materials, commonly used in powder handling. Ideal when limiting spillage is important.
- Belt Feeder: Ideal for controlling the flow of bulk materials from a hopper that has a long, slotted outlet.
- Rotary valve: Maintains consistent pressure while feeding material into a pneumatic conveying system. It also functions as an airlock, preventing air leakage while allowing material flow.
- Vibratory Pan Feeder: Uses vibration to move materials, suitable for fragile substances to prevent degradation.
- Apron Feeder: Heavy-duty device designed for handling abrasive materials.
Material Transfer Equipment
Mechanical Conveyors
Mechanical conveyors are the backbone of material transfer in bulk handling systems, available in various forms to suit different materials and applications:
- Belt Conveyors: Versatile and widely used for transporting bulk materials both horizontally and with moderate slope over long distances.
- Screw Conveyors: Ideal for conveying over shorter distances when containment is important.
- Bucket Elevators: Used for vertical movement of bulk solids.
- Drag-Chain Conveyors: Efficient for handling granular materials.
Pneumatic Conveyors
Pneumatic systems use air or some other gas to transport bulk materials through pipelines. They are highly effective for moving fine powders or small granular materials, offering flexibility in routing, elimination of spillage, and isolation from the ambient environment.
Specialized Equipment
Mass Flow Portable Containers
Designed to promote uniform, unrestricted flow, mass flow containers prevent issues like arching, ratholing or segregation, which are common in poorly designed hoppers.
Mass Flow Tumble Blenders
These blenders ensure homogeneous mixing of bulk materials, which is crucial in industries such as pharmaceuticals and food processing.
Anti-Segregation Distributors
These distributors help maintain material uniformity during handling, preventing separation due to differences in particle size or density.
J-Purge® Gas Introduction Systems
These systems introduce gases into the material flow, allowing effective devolatilization of polymers, uniform drying of flakes, efficient conditioning of bulk solids, etc.
Solids Pump®
These systems are specialized devices designed to precisely control bulk solids flow into a pressurized environment, making them ideal for high-precision applications.
Mass Flow Y-Branch Transfer Chutes
These specialized chutes facilitate material transfer between different parts of the handling system, promoting smooth flow and minimizing wear.
Measurement and Testing Equipment
Shear Testers
Ring and translational shear testers such as the Jenike Shear Tester measure the flow properties of powders and bulk materials, including internal friction, wall friction, and cohesion—critical for designing effective handling systems.
Specialized Bulk Material Testers
Specialized testers evaluate powder flow characteristics, segregation potential, permeability, compressibility and other critical parameters, helping optimize system design and operational efficiency.
Optimizing Your Bulk Material Handling with Jenike & Johanson
The efficiency and reliability of bulk material handling systems hinge on the proper selection and integration of various pieces of equipment. At Jenike & Johanson, we specialize in engineering solutions that optimize material flow, reduce downtime, and enhance process efficiency. Whether you’re facing challenges with storage, conveying, or flow control, our team of experts is ready to assist.
Contact us today to discover how we can support your bulk material handling needs and drive your operation toward greater productivity and reliability.