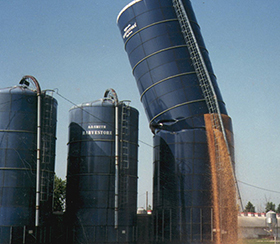
Co-Author: Atul Kulkarni
Bunkers, bins and silos are containment structures used to store bulk solids. A common component in these structures is a metallic cylinder where most of the bulk solid is stored. One of the critical failure modes for metal cylinders is local buckling. Buckling is the result of structural instability, making the structure unable to withstand the imparted compressive loads. This normally results in large deformations where the structure finds a new geometry of equilibrium. Generally, when a structure fails by buckling, the compressive stress does not exceed the metal yield stress but exceeds the critical compressive stress, which dependents on the structure’s geometry and material properties.
The critical compressive stress for cylindrical shells depends on the shell geometry (radius and thickness of shell) and properties of the material of construction. The theoretical value for elastic local buckling stress of an axially compressed cylinder assumes a perfect shell free of imperfections. However, shells are very sensitive to imperfections. Surface imperfections include dents, wrinkles, uneven thickness loss etc. Surface imperfections always exist in cylindrical shells fabricated in structural fabricating shops. Real cylindrical shells that are axially compressed usually buckle at stresses smaller than the theoretical value.
To explain the importance of surface imperfections in thin shells, we will use the example of a soda can. When an empty soda can is loaded axially, it can sustain a higher load compared to a soda can that has experienced a level of deformation (e.g. dent or dimple). To demonstrate this, we performed a simple experiment by axially loading three empty soda cans (see video below). One of the soda cans without any noticeable surface imperfection was loaded until it failed by buckling. We repeated this experiment with the other two soda cans; however, for the second one we introduced very small surface imperfections (e.g. dents) and for the third one the level of imperfections was even higher. The values at which each can failed by buckling are presented in the table below. This clearly shows how the buckling capacity is significantly affected by surface imperfections.
In bins and silos the shear traction imposed by the stored material on the internal face of the cylinder wall produces compression along the height of the cylinder. Roof loads and self-weight also contribute to the compressive loads imposed on the cylinder walls. This compression can cause local buckling on the cylindrical shell if the shell is not thick enough. Once the cylinder in the storage structure is sufficiently over-stressed, irreversible deformation occurs. Sometimes, fill and discharge cycles can cold-work these buckles back-and-forth. This can actually rupture the wall if thin enough, since the bending stresses become very high. Unless this problem is corrected, silo collapse is inevitable, which often results in significant property damage and possible loss of life.
It is important that all personnel in industrial facilities be vigilant about these signs of distress (e.g. buckles, dents, holes) and not ignore them so appropriate actions can be taken to avoid tragic events due to structural failures.